Waste not, want not: increasing titanium and aluminium circularity
Airbus is committed to improving the use, reuse and recycling of manufacturing materials
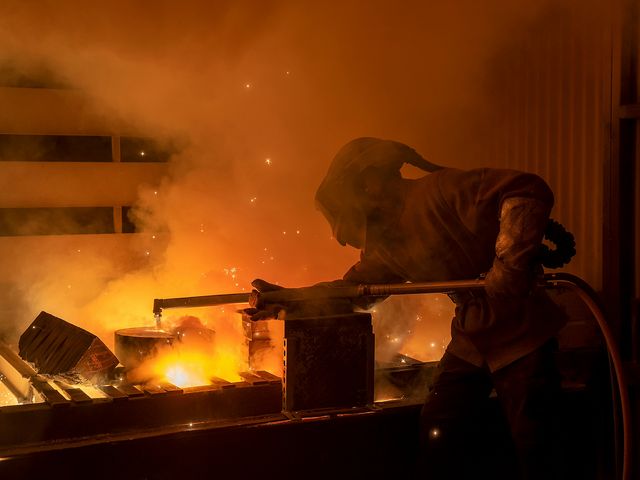
Airbus is reshaping the lifecycle of materials used in aerospace manufacturing. With service lives upwards of 20 years, aircraft have always been designed for longevity and optimised resource use. Now, thanks to advances in key technologies, Airbus is improving its ability to reduce aluminium and titanium consumption during manufacturing, salvage parts from decommissioned aircraft, and recycle metals. It is a gamechanger for these two metals.
What is circularity?
Circularity is a model of production and consumption that seeks to optimise resource use and minimise waste. This is especially pertinent for metals, which for the most part are infinitely recyclable, without any deterioration in quality. However, while circularity and recycling efforts have led to an increase in the use of recycled materials, this growth continues to be outpaced by demand for virgin metals.
Airbus is dedicated to advancing materials circularity within the aerospace value chain, with a particular focus on two metals: titanium and aluminium. Titanium is one of the primary metals of structural aerospace manufacturing, with its alloys primarily used for pylons, engines and landing gear. Aluminium, for its part, is used extensively to form aircraft fuselages, wing structures and interiors. Both metals are lightweight, resistant to corrosion, and have a high strength-to-weight ratio. Titanium is also resistant to high temperatures and has good fatigue resistance.
Efforts at Airbus to increase the circularity of these two metals are present throughout the value chain. The goal is to increase circularity through the ten ‘Rs’, which are found in how products are designed (refuse, reduce, rethink), how their lifespans are extended (reuse, repair, refurbish, repurpose and remanufacture), and how the end-of-life process is dealt with (recycle and recover). Many people may already be familiar with a simplified version of this: reduce, reuse, recycle.
Achieving true circularity for aerospace-grade titanium and aluminium – also called closing the loop – is a complex undertaking that requires a collaborative approach. Airbus is thus actively working on a variety of initiatives across a wide ecosystem, including with raw material suppliers, component manufacturers, recycling specialists and industry partners.
Exploring technologies to reduce metal consumption
While 3D printing is not a new manufacturing concept, Airbus has been taking steps to use a specific kind of 3D printing technology – called additive layer manufacturing (ALM) – to produce aircraft parts from titanium with minimal waste. Instead of forging a part from a larger amount of material or milling it down and ending up with scraps – in other words, a subtractive process – additive layer manufacturing allows for parts to be manufactured using only what material is needed.
Indeed, ALM is a win-win situation: the process uses less raw material, which means lower production costs. Two primary forms of ALM are used in aerospace manufacturing, reducing raw material use in different ways. The first is powder bed fusion (PBF), which uses laser beams to melt powdered titanium into a desired shape. This allows a part to be constructed by creating layers as thin as 0.1mm on top of each other.
This technology is now being used by Airbus to create the 32 door latch shafts needed for each A350 aircraft. Before, the latch shaft of the A350 was made using ten separate parts that were assembled together. Now, with ALM, there is only one integrated part, which weighs 45% less compared to latch shafts made using a traditional forging process. In real terms, that amounts to a weight savings of just over four kilograms per aircraft, which is the equivalent of saving up to 126,000 kilogrammes of CO2 emissions over a 20-year aircraft lifespan.
The second ALM method is directed-energy deposition (DED), which is used to create large and regularly shaped parts by using a laser to melt a titanium wire and then deposit it in place. This technique results in a ‘near net shape’ part, meaning it is very close to its final shape but still must be fully machined before being ready for installation. This is an improvement over traditionally forged parts, where several centimetres of material usually need to be removed during machining.
In July 2023, the first two DED-manufactured parts were installed on an A350. DED is classified as the most promising ALM technology for Airbus because the development lead times are quicker than those for traditional forgings, and it also helps relieve pressure on titanium supply chains.
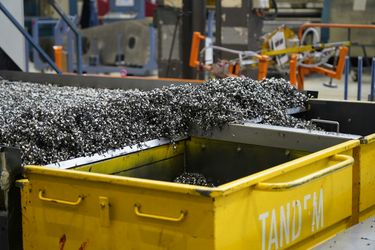
Saving metal scraps from the junk pile
Although new manufacturing techniques can reduce metal consumption, there will always be some level of waste during production. To counter this, Airbus is investing in recycling titanium production floor scraps. Titanium scraps are critical to manufacturing new ingots because aerospace-grade titanium is not pure – it is made of a mix of virgin alloy (titanium sponge) and recycled titanium. Since 2024, a company called EcoTitanium* has been recycling titanium scraps gathered from engine pylon production at Airbus’ Saint-Eloi factory in Toulouse, France. As of January 2025, 460 tonnes of scrap had been collected from Airbus sites in France for processing by EcoTitanium, and the company has been working to establish the closed loop recycling of titanium scraps from Premium Aerotec sites in Germany.
Moving to the end of the lifecycle, the manufacturing of the first ingot containing end-of-life titanium from an Airbus pylon was completed by EcoTitanium in June 2025, under the lead of Airbus and in collaboration with IMET Alloys. The ingot, which will be used by metals specialist Aubert & Duval to manufacture new titanium-forged airframe parts, is the first instance of secondary material from end-of-life scrap being reused in manufacturing aerospace-grade material.
EcoTitanium is the first venture in Europe to offer recycled aerospace-grade titanium, with the potential to produce up to 75%-recycled titanium ingots, which will then be reallocated to Airbus production programmes. EcoTitanium’s manufacturing process uses four times less energy than the traditional method of using titanium sponge, leading to a reduction in carbon emissions.
In addition to these titanium initiatives, Airbus has also teamed up with key aluminium producers Constellium and Novelis to establish closed loop recycling of aluminium production scrap, with more similar industry partnerships in the works. Five Airbus sites, working in collaboration with external machinists, are part of an initial pilot that aims to improve traceability of aluminium scrap and develop a standard calculation for determining the ratio of recycled content. The project involves onboarding the machinists, who produce the scrap; the scrap dealers, who ensure collection and distribution of the scrap and play a crucial role in ensuring traceability; and the melters. Putting this closed loop recycling process in place will be an important step toward improved traceability for aluminium and for industry alignment on how it is handled. By the end of 2026, all aluminium from Airbus sites will be included in the closed loop.
As with titanium, expanding the recycling and reuse of aluminium beyond manufacturing is also key to creating circular models for the aerospace industry. Tarmac Aerosave (a company jointly owned by Airbus, Safran and Suez) has partnered with Constellium to recycle fuselages into new aluminium alloys that meet aerospace manufacturing specifications. The two companies recently announced a milestone in their partnership after successfully recycling and remelting aluminium from an aircraft fuselage into a new, high-performance alloy suitable for future aerospace applications. This is a promising development, as recycling aluminium uses only 5% of the energy required for primary production and emits 95% fewer CO₂ emissions.
Salvaging usable parts from decommissioned aircraft
While closed loop and end-of-life recycling initiatives reduce waste from manufacturing parts, these parts often have long lives – sometimes longer than an aircraft itself. Enter VAS Aero Services, a subsidiary of an Airbus-owned company called Satair that offers manufacturers and operators a range of aircraft parts and services, including an end-of-life dismantling programme. Practically speaking, once an aircraft has reached the end of its time in service, it is dismantled by VAS Aero Services and the parts are sorted into two categories: those that can be reused are sold to airlines and lessors, and those that cannot be resold are scrapped and recycled.
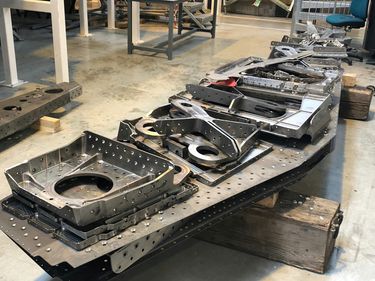
While recycling can significantly reduce waste and carbon emissions over a material’s lifecycle, reusing parts is the most sustainable process of all as it extends their lifetime. Depending on the type of aircraft and its age, VAS Aero Services can recover anywhere from 300 to 6,000 parts for resale. The most common parts that are sold to be reused for aircraft repairs are structural components like the engines, landing gear and auxiliary power unit.
Because every single part on an aircraft has to be traceable, VAS Aero Services is responsible for verifying the paperwork, serial number and lifetime flight cycles allowed for each individual part. It is time-consuming work but one that allows the business to extract the maximum financial value from a decommissioned aircraft while reducing its lifecycle environmental footprint.
Closing the loop: how far left to go?
Achieving a completely closed loop where 100% of all materials in an aircraft’s value chain are recycled or reused within the industry is an ambitious long-term vision. Progress towards this goal has been challenging for the aerospace industry due to the stringent safety and performance requirements of aerospace manufacturing.
“Creating a circular economy for aerospace materials is a complex journey, but we are making significant progress,” explains Isabell Gradert, Vice-President of Central Research & Technology at Airbus. “We are embracing innovative approaches to reducing waste and optimising resources across the value chain. Continued collaboration and dedication will be required to fulfill our long-term vision of closing the loop.”
Despite the breadth of the challenge, Airbus remains committed to increasing the circularity of different manufacturing materials as part of the Company’s broader ambition to pioneer sustainable aerospace. By focusing on intelligent design, efficient resource use and advanced recycling technology, Airbus is not only reducing emissions from its products but also enhancing the resilience and efficiency of its own operations.
*EcoTitanium is a joint venture by Aubert & Duval of France, French ecological transition agency ADEME and regional bank Crédit Agricole Auvergne. Airbus is a joint owner of Aubert & Duval along with Safran and Tikehau Capital.
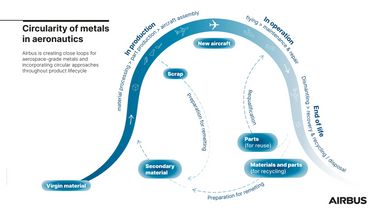
Discover more Innovation news
Continue Reading
Powering production and protecting people with exoskeletons
Web Story
Innovation
Discover how Airbus is revolutionising aircraft production with industrial exoskeletons that improve ergonomics and safety for workers.Airbus and MTU Aero Engines advance on hydrogen fuel cell technology for aviation
Press Release
Innovation
Airbus and Critical Software explore strategic partnership in embedded software…
Press Release
Innovation
Strengthening Europe's sovereignty: Airbus and Quantum Systems work on ecosystem for…
Press Release
Defence
Airbus at Paris Air Lab 2025: Discover Tomorrow, Today
Web Story
Innovation