Testing the open fan’s promise
Using the wind tunnel to explore propulsion options for a next generation aircraft.
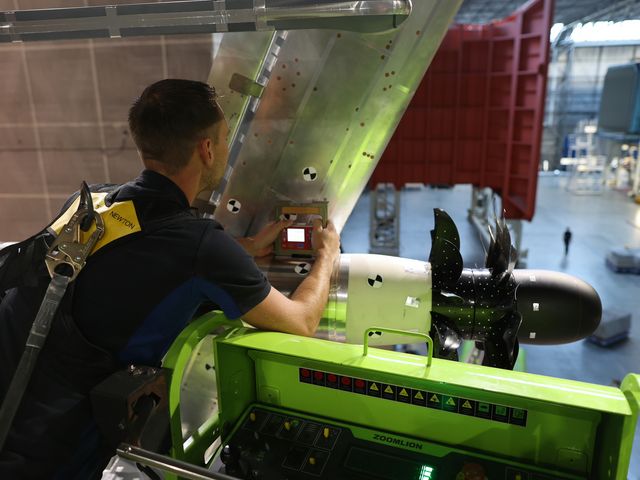
New propulsion systems including the open fan could further increase the fuel efficiency of a next generation aircraft. Airbus and engine partner CFM International are testing an open fan demonstrator, part of CFM’s RISE program, to explore its aerodynamic profile, acoustic footprint and ease of integration.
Next-generation aircraft propulsion systems play a big part in the aviation industry’s net-zero ambition by 2050.The open fan engine architecture is one such promising technology. It combines the fuel economy of a turboprop with the performance and speed of a turbofan. Ahead of real-world flight testing, Airbus and engine partner CFM are running wind tunnel tests on an open fan demonstrator to examine its aerodynamic and acoustic performance.
Compatible with alternative energy sources
Designing a future Airbus aircraft starts with reducing its fuel consumption. Improved aerodynamics make a big contribution, but the propulsion system can make a significant difference too. The open fan’s aerodynamic profile, acoustic footprint and ease of integration will all be decisive when it becomes time to choose between this technology and its rival, the ultra-high bypass turbo fan.
To that end, for the last three years Airbus partner CFM (a joint venture between GE Aerospace and Safran Aircraft Engines) has been developing an open fan demonstrator through its RISE technology demonstration program, or Revolutionary Innovation for Sustainable Engines.
The RISE program’s goals include reducing fuel consumption and CO2 emissions by more than 20% compared to today’s most efficient engines, as well as testing compatibility with alternative energy sources including sustainable aviation fuels (SAF) and hydrogen. The programme is supported by funding from the European Clean Aviation framework, the French Civil Aviation Authority (DGAC), and CORAC, the French Civil Aviation Council.
Wind tunnel tests provide highly accurate data
Airbus has partnered with CFM to evaluate open fan’s potential for use on a future aircraft. Before flight testing can begin, the open fan architecture and its integration onto the aircraft are subjected to wind tunnel testing. This test phase deploys two ‘minimum body models’: a 1:5.5 scale model for high-speed testing and a 1:7 model for low-speed testing.
Each model is tested both alone and with a scale-model wing to evaluate how the two interact. For the low-speed model, testing is extended to high-lift devices such as flaps and slats. The tests are held at wind tunnels belonging to French aerospace lab ONERA (high speed) and DNW, a Dutch-German facility located in the Netherlands (low speed). Both produce highly accurate data.
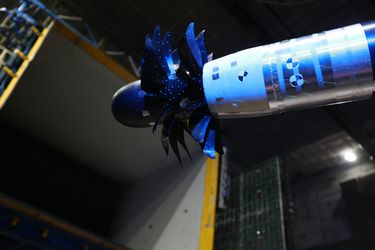
The high-speed tests were run at ONERA in early 2024. They gathered experimental data, enabling researchers to study the models’ installation effects and propeller performance. Then tests replicating take-off and landing were conducted at DNW from September to late November 2024. They focused on the open fan’s aero-acoustic performance and interaction with high-lift devices.
As open fan engines are unducted (they dispense with the cowling of conventional jet engines), addressing the noise of their larger rotor blades requires innovative design choices and new technologies at engine and aircraft level. Nonetheless the engines must still conform to acoustic regulatory and certification requirements.
Towards flight testing
After over 500 hours of testing, this ‘minimum body’ campaign – just the first – is coming to an end. The next step is to assess how an open fan propulsion system affects aircraft performance, using 1:11 (high speed) and 1:14 (low speed) full aircraft models. These models will be tested at ONERA’s high-speed wind tunnel and Airbus’ low-speed facility in Filton, UK, in 2026. Their design and production is already in progress.
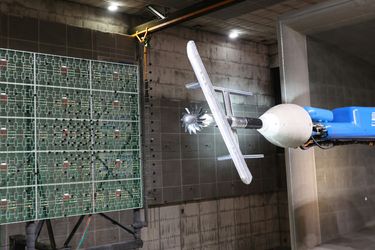
Open fan testing will meet full-scale reality by the end of the decade, when a fully functioning engine will be fitted to an A380 flight test aircraft operating out of Toulouse, France. The process of modifying the aircraft to host the engine has already begun.
What is wind tunnel testing?
Wind tunnel testing is crucial for validating digital simulation and modelling. By blowing air over scale models, engineers observe and measure the forces of lift and drag, as well as stability and control.
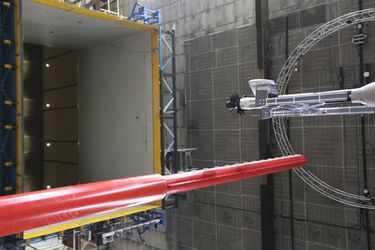
This helps them to identify potential design flaws and optimise the aircraft's shape for better performance and fuel efficiency, before a full-size, expensive prototype is built. Wind tunnels simulate various flight conditions, helping to ensure the aircraft can handle different speeds, altitudes, and even challenging weather, ultimately leading to safer skies.
Discover more Innovation news
Continue Reading
Powering production and protecting people with exoskeletons
Web Story
Innovation
Discover how Airbus is revolutionising aircraft production with industrial exoskeletons that improve ergonomics and safety for workers.Airbus and MTU Aero Engines advance on hydrogen fuel cell technology for aviation
Press Release
Innovation
Airbus and Critical Software explore strategic partnership in embedded software…
Press Release
Innovation
Strengthening Europe's sovereignty: Airbus and Quantum Systems work on ecosystem for…
Press Release
Defence
Airbus at Paris Air Lab 2025: Discover Tomorrow, Today
Web Story
Innovation