Flying high in Airbus simulators
Airbus’ flight simulators help validate new systems and improve airborne safety
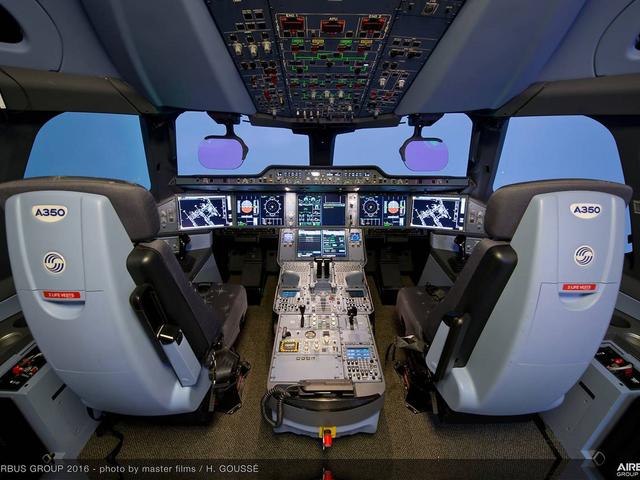
For 11 hours each workday – and sometimes longer – the flight simulators at Airbus’ Single Test Centre, or STC, are kept busy.
It’s at the Saint-Martin campus in Toulouse, France that simulators for all Airbus commercial aircraft are housed – from in-development models that have yet to take wing, through each and every in-service model, to the Airbus aircraft of yesteryear no longer in production.
Some of the 10 simulators in building M24 are dedicated to just one aircraft family, such as the A350 XWB, while others can be configured for different variants across families. Each simulator was made in-house by Airbus personnel; the oldest one, for Airbus’ cornerstone A300/A310 aircraft, is more than 40 years old.
Unlike the simulators used at Airbus Training Centres around the world that feature the latest certified systems for a given aircraft – and which are used by airline pilots to familiarise themselves with a jetliner type – the vast majority of STC simulator users are testers, usually Airbus engineers validating new systems and upgrades to existing ones.
These engineers also perform human factor trials, observing how flight crews react to various alarms and displays.
While a typical session in an Airbus flight simulator lasts around two and a half hours, a 72-hour multi-leg world tour is possible.
Prior to an airliner’s first flight, STC simulators let Airbus engineers safely evaluate manoeuvres and scenarios that would be too dangerous to undertake in an actual flight; they also allow test flight crews to become familiar with how a new aircraft and its systems will perform during the actual test flight campaign. In addition, Airbus has been granted authority by the European Aviation Safety Agency and America’s Federal Aviation Administration to certify certain aircraft systems using these high-tech simulators.
Engineers can customise the simulators to display airport runways of various lengths and elevations to test aircraft performance in specific scenarios that can include simulated weather conditions such as snow, fog, rain, wind and turbulence. While a typical ‘flight’ in one of the simulators lasts around two and a half hours, a 72-hour world tour is possible – a multi-leg trip that would generate up to 100 gigabytes of performance data.
While the setups at Airbus’ STC and in training centres around the world feature simulated cockpits powered by computers running real-world avionics software, only STC simulators can be connected to actual working systems on a ground-based Iron Bird – a ‘skeletal’ form of an aircraft in which major working components (such as hydraulics and flight control components) are installed in the approximate locations found on the actual airframe.
Read more Commercial Aircraft news
Continue Reading
Avolon orders 15 A330neo and 75 A321neo Airbus aircraft
Press Release
Commercial Aircraft
Avolon ordered 15 A330neo and 75 A321neoAirbus completes the first horizontal stabiliser for the A350F freighter in Spain
Press Release
Commercial Aircraft
Flight control system: more redundancy to enhance resilience
Web Story
Safety
STARLUX orders 10 more Airbus A350-1000s
Press Release
Commercial Aircraft
EGYPTAIR discloses order for an additional 6 Airbus A350 aircraft
Press Release
Commercial Aircraft