Flight control system: more redundancy to enhance resilience
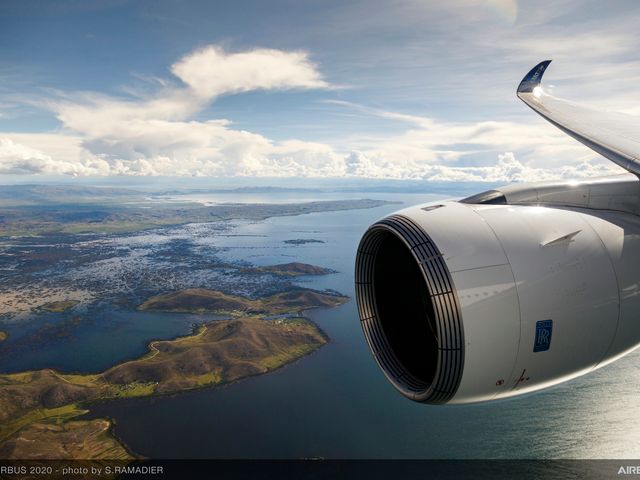
Airbus’ innovative 2H2E flight control system blend of hydraulic and electrical power proved its remarkable resilience during a major A380 engine failure in 2010. This event showcased a new standard in aviation safety, now integral to modern Airbus aircraft.
On 4 November 2010, an A380 suffered a major engine explosion shortly after takeoff. High energy debris struck the plane, causing significant damage to the aircraft’s structure and cutting around 350 wires.
Despite the serious damage caused by this uncontained engine rotor burst, the crew was able to fly the plane back to the airport. This was possible because the A380’s key safety systems, including the autopilot and the flight envelope protections – a system that prevents the aircraft from making any dangerous moves, like flying too fast or too slow – continued to work.
In addition to the flight crew performance, this outstanding outcome was made possible thanks to the plane's robust design, and more specifically its 2H2E flight controls system architecture. Thanks to this architecture, two hydraulic systems are backed up by two electrical systems. This concept was developed in the 1990s and first implemented in large civil air transportation airplanes on the A380.
At this time, Airbus developed a new concept for moving the aircraft's flight control surfaces: the Electro-Hydrostatic Actuator (EHA). On large aircraft, flight control surfaces are moved by devices that create motion. Typically, these are powered by a central hydraulic system. The EHA, however, is a device that uses electrical energy to create this movement instead of hydraulic power.
This invention allowed for the reduction of the number of hydraulic circuits needed by combining electrically powered actuators and conventional servocontrols, leading to the implementation of the 2H2E architecture on the A380 instead of a classical architecture with three hydraulic circuits (3H architecture):
- 2H for 2 segregated hydraulic circuits
- 2E for 2 segregated electrical systems
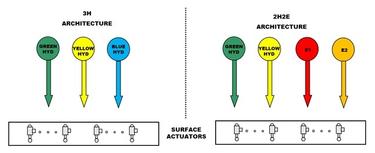

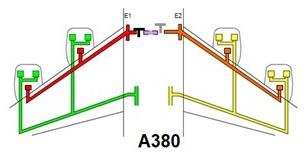
Finally, the redundancy is improved with two electrical systems (E1 in red and E2 in orange in the figure above) replacing one hydraulic system (the blue one in the figure above). Thanks to the 2H2E architecture, the following surfaces remained available during the incident cited at the beginning of this article:
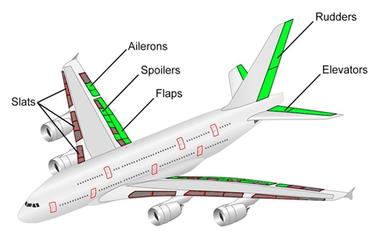
The 2H2E architecture introduced on the A380 represents a major safety advancement. It is now a standard for Airbus building on the A380's model for the A350 and the A400M.
Our latest safety news
Flying with lithium ion batteries in passenger luggage
Web Story
Safety
Your guide to flying with lithium ion batteries safely. Learn the rules for carry-on vs. checked baggage and what to do in an emergency.Flight control system: more redundancy to enhance resilience
Web Story
Safety
Aviation safety trends show need for continued vigilance
Web Story
Safety
How Airbus is training the current and next generation of helicopter pilots and…
Web Story
Helicopters
Airspeed information, whatever the conditions
Web Story
Safety