Quick News-August 2020
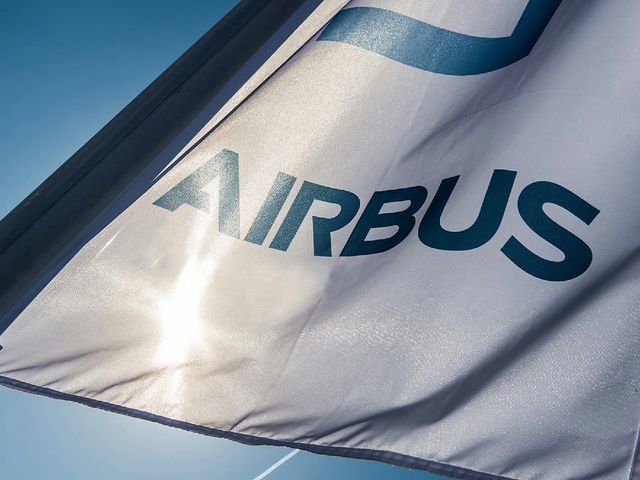
First metal cut achieved for the A321XLR’s Rear Centre Tank section
Following the recent ‘first metal cut’, production of the first Rear Centre Tank (RCT) for the new long range A321XLR is now underway. The RCT, which is unique to this variant, is a permanently installed high-capacity fuel tank which makes maximum volumetric use of the aircraft's lower fuselage. The RCT structure which is integrated in fuselage Sections 15 and 17 is located behind the main landing gear bay and holds up to 12,900 litres – which is more fuel than several optional Additional Centre Tanks (ACTs) combined could hold previously in the A321 Family. Moreover, since the RCT takes up less space in the cargo hold, it frees-up underfloor volume for additional cargo and baggage on long range routes of up to an unprecedented 4,700nm. Premium AEROTEC, which was commissioned by Airbus in September 2019 to manufacture the RCT, is currently completing the structure's sub-assembly at its factory in Augsburg, Germany. This phase involves production of the other RCT parts, followed by structural assembly, systems equipping and testing prior to delivery to Airbus' major component assembly (MCA) facility in Hamburg early next year, where the tank will be integrated into the aircraft's rear fuselage. The A321XLR, the next evolutionary step in Airbus' single-aisle products, has been designed to maximize overall commonality with the rest of the A320neo Family, while introducing minimal changes needed to give the aircraft an Xtra Long Range with increased revenue payload and best travel experience.
BelugaXL enters into service in Getafe
The BelugaXL recently expanded its operational reach by adding Airbus’ facility in Getafe, Spain to its network. This aircraft “no.2” – the second to fly – is working alongside the five A300-600-based BelugaST predecessors. Today the new aircraft operates several flights per week, transporting all Airbus family horizontal tailplanes and A350 XWB Section 19 (manufactured in Getafe) and A350 XWB wing lower covers (manufactured in Illescas) from Getafe to other Airbus sites in Toulouse, Hamburg and Broughton. The Getafe site itself also features a 7,200m² hangar which is dedicated to the Beluga fleet loading and unloading operations. In addition to its Getafe missions, the new transporter is also ferrying other major aircraft parts between the various Airbus sites.
The first BelugaXL flew in July 2018. This aircraft “no.1” is tasked with ongoing flight tests and evolutions. Entry-into-service of the first operational BelugaXL (aircraft “no.2”), took place from Toulouse to Broughton on 9th January this year. Aircraft “no.3” made its first flight in July this year and will enter service in Q4 2020.
By 2023 a total of six A330-based BelugaXL aircraft will be operating between the European Airbus sites. Launched in November 2014, the BelugaXL programme was awarded Type Certification by the European Aviation Safety Agency (EASA) in November 2019, following an intensive certification test campaign which saw it complete more than 200 flight tests, clocking over 700 flight hours.
Link to photo 1 Link to photo 2
Airbus proposes MEDEVAC conversion of passenger aircraft
A multi-functional team composed of Airbus Commercial Aircraft, Airbus Defence and Space and Airbus Helicopters has proposed a solution to quickly convert passenger aircraft into a Medical-Evacuation (“MEDEVAC”) configuration to offer to customers worldwide. The French DGS (Direction Générale de la Santé) has actively supported Airbus by providing all the medical specifications associated with Covid-19 patients in intensive care and low care. In six weeks, the team defined solutions based on A330/A340 platform which is capable of carrying COVID-19 patients in intensive care over a long-range distance. The concept has been subsequently fine-tuned and Airbus is now in a position to offer a mature solution to any customers wishing to perform MEDEVAC operations.
Link to photo 1 Link to photo 2
Airbus Flight Training’s COVID taskforce prepares the way for return to global operations
Airbus Flight Training’s dedicated COVID taskforce is proactively implementing measures to guide its customers and stakeholders through the crisis and to prepare them for the resumption of normal operations worldwide. To this end, the taskforce has recently rolled-out various measures throughout Airbus’s global training network, National Aviation Authorities and Airbus operators. As well as basic solutions (such as the provision of health & safety guidelines; maintaining a ‘ready’ core team in each training centre and providing guidance to national Authorities), Airbus Flight Training also rolled-out several strategic solutions. The latter include: further deployment of classroom instruction via video-conferencing to allow ab-initio theoretical training to continue in the flight school network; increased distance-learning in the advanced flight training phase called “Extended Flight Training Distance” (EFTD) learning; renewed recency programme which is adapted to the ‘new reality’; and the ‘Airbus Pilot Re-launch Program’ (APRP), providing several solutions for training for pilots who have been grounded for an extended period.
The EFTD learning solution, which involves virtual classroom instruction, allows the instructor to hold a class by video, with all pilots or cadets connected in an interactive video environment. EFTD complements the already existing e-learning modules covering "system knowledge", the initial part of the Type Rating training for the A320, A330 and A350. The virtual classroom instruction – which is designed to complement full-flight simulator training – was created and written by Airbus, and approved by the French national aviation authorities (DGAC). Meanwhile, APRP for pilots who have not flown for a few months, provides variable training scenarios to adapt to the individual, and incorporates the Competency-Based Training Assessment philosophy. It takes place over one day including both theoretical and practical (simulator) training.
Link to photo 1 Link to photo 2
EASA approves Airbus’ maintenance “Synchronous Distance Learning”
To support Airbus’ customers and offer them the opportunity to optimise this period of travel restrictions, Airbus Training Services has set up and obtained EASA-approval for a “Synchronous Distance Learning” solution for theoretical certifying maintenance courses and non-certifying courses. Customers will be able to participate to local examination sessions where Airbus stations are available – with the support of its Field Service Representatives who are trained and registered to be an “examination invigilator”. Once travel restrictions are lifted and whenever practical training is required, the training effort will be limited to organising these practical sessions. In short, this distance learning solution allows customers to perform theoretical maintenance training locally, led by a real-time remote Airbus instructor, to receive local examination sessions managed by a local Airbus invigilator.
Link to photo 1 Link to photo 2
Airbus Miami Training Center launches scholarships for A320 Type Rating Qualification and Maintenance Technician qualification
As part of its ongoing efforts to support the aerospace community during the Coronavirus pandemic, the Airbus Training Center in Miami (ATC) launched an A320 Type Rating Qualification course scholarship for student pilots and aircraft maintenance technicians in the United States. The initiative is part of a collaboration between the Miami ATC, OBAP (Organization of Black Aerospace Professionals), WAI (Women in Aviation International), Embry-Riddle Aeronautical University and Lynn University to further support the aviation industry's diversity and future needs. In total, 16 students will benefit from the scholarships. The pilot students will be qualified to fly an A320 upon successful completion of the training, and the maintenance students will have the opportunity of becoming candidates for entry-level maintenance positions with Airbus' airlines and MRO customers. The Airbus Training Center in Miami, Florida, which provides training for Airbus customers' flight and cabin crew as well as maintenance personnel, trains approximately 2,200 trainees a year.
Satair’s ‘AutoStore’ brings efficiency and space at its Hamburg facility
Airbus’ parts logistics subsidiary Satair has introduced an all-new, automated storage system, “AutoStore”, at its facility in Fuhlsbüttel, Hamburg. The new warehouse system accommodates three times as many small parts as in the past, without the need to enlarge the existing 36,000sq m logistics centre. Compared with a maximum of 100 “picks” from the shelves per hour previously, with new robots the warehouse can now handle 500 picks. Moreover, each day 10,000 orders can be dispatched – compared with 3,000 previously. The AutoStore system, developed in cooperation with the logistics service provider DB Schenker, enhances delivery quality and on-time delivery with greater flexibility while reducing overall logistics costs. At the heart of AutoStore is a three-dimensional grid, in which up to 560,000 small parts can be stored in individual ‘bins’ which are stacked in a high density layout. On the surface of this grid, 40 robots now move along the warehouse, pick the respective bins and transport the parts to an ergonomically adapted packaging station – avoiding the need for people to physically go to each of the shelves. Furthermore, routine orders can now depart Satair's AutoStore within 24 hours, urgent orders for AOGs (Aircraft on Ground) are ready for dispatch within four hours. Overall the facility’s processes are more robust, with delivery reliability being guaranteed even by unpredictable volume changes.
Link to photo 1 Link to photo 2 Link to photo 3
Skywise Parking Management app eases aircraft logistics and return to service
With Airbus’ new Skywise geospatial app, airlines can now tag their grounded aircraft, and virtually park them into airports/stations (hangar, gate, taxiway, etc.) – using the Skywise open data platform. With the app, airlines can rapidly extract contextual data such as an aircraft’s age, latest and next checks, last major assembly overhaul, and more. This allows them to efficiently decide where to store each individual aircraft, and in what order. The app was developed in the frame if the COVID‐19 circumstances which has forced airlines to ground much of their fleets. The app eases the task of tracking down and knowing which of their aircraft are stored in which location, and which maintenance tasks needs to be carried out to uphold airworthiness. Furthermore, once passenger demand returns, airlines will need to identify the optimal aircraft to bring back into service and generate a checklist of the necessary maintenance tasks – another challenge which this app makes much easier for airlines solve.
NAVBLUE launches RunwaySense to assess and report runway conditions using the aircraft as a sensor
NAVBLUE, Airbus’ dedicated flight operations subsidiary, has launched a new service called “RunwaySense”, which allows airlines and airports to accurately assess and report runway conditions by using Airbus aircraft ‘as a sensor’. Using the new system, airports can use the aircraft data to inform their runway clearing operations, which permits better timing of the runway clearing activities as well as more targeted application of de-icing chemicals. Furthermore, with the mandatory ICAO Global Reporting Format (GRF), due to come into effect in November 2021, this data contributes to airports reporting requirements with accurate, near real-time runway performance information. Airlines can also use this data to better monitor their operations as they share the data which their aircraft have generated internally, or access data generated by other operators. RunwaySense is based on BACF+ (Braking Action Computation Function), software released by NAVBLUE in 2019 on the Airbus single-aisle family. It is also the first of NAVBLUE’s airport-focussed solutions.
Airbus Interiors Services agreement with Aerkomm on K++ connectivity installation on retrofit, for A320 family
Airbus Interiors Services (AIS) and Aerkomm have signed an agreement enabling the Aerkomm K++ in-flight connectivity (IFC) solution installation on the Airbus A320 Family aircraft, in retrofit. AIS will develop, install and certify the Aerkomm K++ system on an A320 test aircraft, to EASA and FAA certification standards. Service Bulletins (SBs) and kits will be provided by AIS, applying Airbus expertise for A320 family customers. The agreement also includes Airbus support for the integration on aircraft, such as, but not limited to, the ARINC 791 structural reinforcements and engineering works. The Aerkomm K++ system will provide passengers with an “at home” network experience using Ka-band technology solution by providing access to on-board Wi-Fi internet connectivity to passengers’ personal devices, including laptops, mobile phones and tablets. This system will additionally provide passengers with access to e-commerce amenities such as in-flight shopping and travel services. The new IFC system will also be compatible with next-generation of satellites.
Airbus introduces Skywise Reliability Premium
Airbus is deploying Skywise Reliability Premium, a set of additional capabilities which supplement those of Skywise Reliability already available and offered with Skywise Core. Skywise Reliability Premium allows airlines to identify and prioritize technical issues across the fleet to save time by getting access to the right first time solution, and easily assess solution effectiveness. It also complements other solutions in Airbus’ wider fleet performance package – including Skywise Predictive Maintenance and Skywise Health Monitoring. Skywise Reliability Premium can help airlines in the current pandemic situation in particular by: reducing engineering analysis time (from three weeks to three clicks); by implementing directly the right service bulletin (SB) during aircraft downtime; by focusing on issues having the biggest cost impact; and by identifying root cause and taking relevant maintenance action.
Your media contacts
Contact us
Martin Fendt
Trade & Technical Press Specialist - Airbus Commercial Aircraft