Above and beyond: Airbus Tech Reps powering the H160's U.S. debut
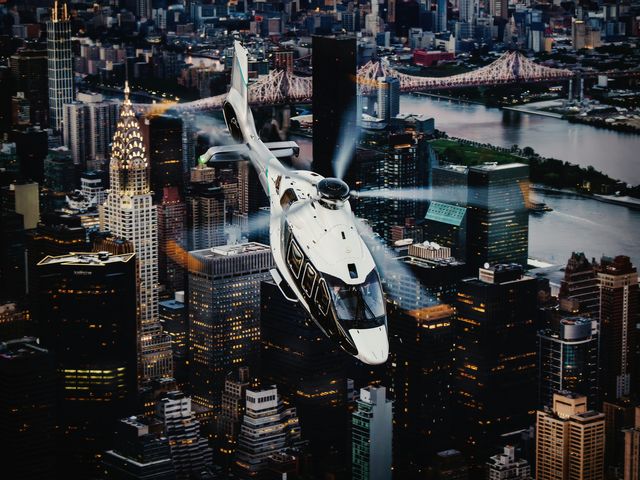
In just one year, the Airbus H160 helicopters have become a prominent sight in North American skies, racking up over 1,500 flight hours. Contributing to this deployment were five dedicated Technical Representatives (Tech Reps), who stepped into action to ensure the helicopters were mission ready.
A multi-layered support system
Airbus Tech Reps form the frontline of aircraft readiness, backed by a support structure designed for swift and effective problem-solving using a tiered approach.
Level 1: The first responders On-site Tech Representatives, such as Gregg Young, an H160 Avionics Regional Technical Representative, serve as crucial first points of contact for customers experiencing technical issues. “I act as a key liaison for providing expert support to both mechanical field representatives and customers operating the H160 throughout the U.S.,” said Young. His expertise lies in diagnosing and resolving intricate avionics and electrical issues, ensuring that the aircraft performs optimally.
Young follows a meticulous process: he gathers detailed information from the customer, reviews relevant technical documentation, assesses the severity of the issue, and offers initial guidance. If necessary, he travels to the customer’s location to provide hands-on support. “My primary focus is to deliver prompt, accurate, and professional support,” said Young.
Level 2: The central role of the Product Support Manager. For issues demanding wider coordination, the H160 Product Support Manager (PSM), Robert Way, serves as the central point of contact. Utilizing global insights from Airbus’ digital data and worldwide network, Robert reviews the technical events, identifying the affected system, and ensuring information is clear before any necessary escalation. Oftentimes, a simple answer is provided. When more information is needed, Robert seeks out an expert for clarification. It’s this approach that successfully resolves many questions.
Level 3: Deep expertise for complex challenges For highly complex issues, particularly with dynamic components, Level 3 experts like Ala Ramadan step in. "If some sort of escalation happens in the field and they need more help, particularly in the dynamic component area, I can help based on my experience," said Ramadan. Level 3 experts analyze the issue, always prioritizing safety, and may consult original design drawings to determine the best course of action, ensuring comprehensive solutions.
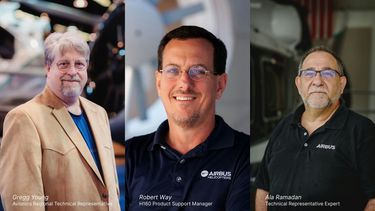
The digital edge: revolutionizing H160 maintenance
The H160 leads in digital maintenance, and its U.S. operations benefit significantly from these advanced systems, which provide real-time diagnostics, reduce downtime, and enhance efficiency.
"The advanced digital maintenance systems integrated into the H160, such as the WACS (Wireless Airborne Communication System), FlyScan, and the features within Helionix, have significantly transformed both my work and the overall maintenance process," said Young.
- WACS System: Enables real-time health monitoring and remote data access for quicker diagnostics.
- FlyScan: Enhances troubleshooting with detailed flight data analysis.
- Helionix Features: Improve situational awareness with easier access to avionics data.
"Overall, these advanced tools have improved the accuracy and speed of maintenance operations, reduced downtime, and enhanced the overall reliability of the H160," said Young. For instance, Helionix alerts allow proactive issue addressing via WACS post-flight, speeding up resolution through data sharing with remote experts.
"Technology has really played a big factor in our jobs and also in ensuring safety,” said Ramadan. “They allow you to contact somebody immediately for a second opinion." The WebTech tool, standard since 2013, facilitates communication and stores valuable history.
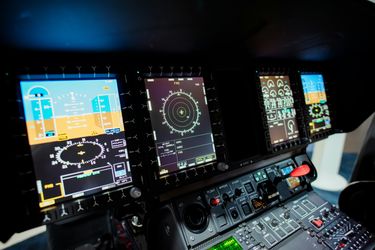
A partnership for success
Airbus Tech Reps are true partners with helicopter operators, aiming to keep aircraft in optimal condition. "The partnership between Airbus Helicopters Tech Reps and customers plays a crucial role in the success of H160 operations," said Young. This involves expert support, tailored solutions, continuous feedback, and operator training. Ramadan shared an instance of traveling to a customer to demonstrate a swash plate design's safety, building trust through hands-on dedication.
The technicians' work directly enables customers to perform critical, often life-saving, missions. "It's really great when you know your aircraft is ready to be able to do a scene mission to rescue somebody,” said Ramadan. “It feels really great. I think anybody will be proud when they know they were involved in missions like this." Way concurs, emphasizing the goal is always to "help the customers."
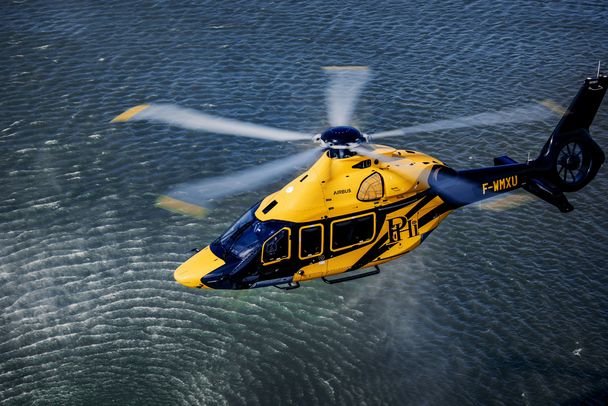
The unseen backbone of aviation safety
The dedication of professionals like Gregg Young, Robert Way, and Ala Ramadan has been critical to the H160’s successful entry into North America, and will continue to be crucial as the aircraft enters into service in greater numbers. Their commitment, supported by digital tools, ensures the Airbus H160 operates at peak performance for essential missions. As Ramadan aptly states, "Teamwork is really the secret to succeed in any mission," and for these technicians, "safety is number one, always."
Copyright Airbus Helicopters 2025
Latest Helicopters news
Continue Reading
Airbus launches H160M flight test campaign
Press Release
Helicopters
Airbus has started flight-testing the H160M Guépard. The helicopter was chosen as a single platform to equip all three branches of the French Armed Forces.Airbus A400M/H225M: A winning duo
Web Story
Helicopters
Nothing can compare to a helicopter's capacity to make lifesaving interventions
Web Story
Helicopters
Airbus and Leonardo to launch NH90 Block 2 studies responding to a request from…
Press Release
Helicopters
Airbus partners with Singapore to explore crewed-uncrewed teaming with the H225M
Press Release
Helicopters