Could hydrogen fuel-cell systems be the solution for emission-free aviation?
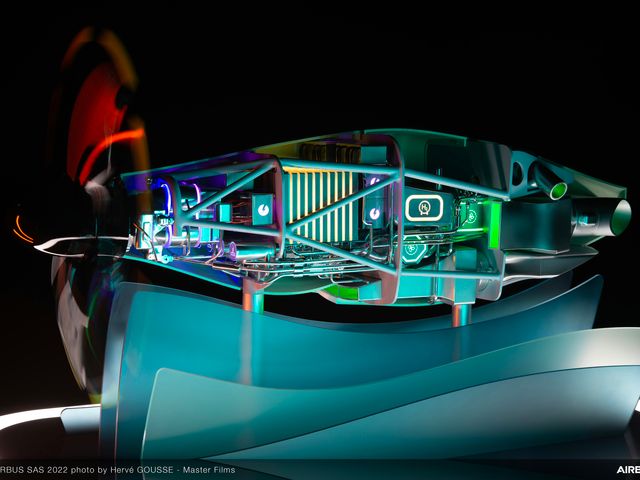
The holy grail of aircraft propulsion is to provide power without any emissions. One of the most promising candidates is the hydrogen fuel-cell. Here we explain how Airbus and its partners are helping to drive the technology forward to be ready for flight demonstrations.
Fuel-cells – originally invented by Sir William Grove in 1838 – generate electricity very efficiently through an electrochemical reaction, rather than via combustion. They also differ from batteries since they require a continuous source of fuel and oxygen (usually from air), whereas in a battery the chemical energy comes from substances which are already present inside the battery. Fuel cells can therefore produce electricity continuously for as long as fuel and oxygen are supplied.
The most promising technology for mobile applications is called Proton Exchange Membrane (PEM). In this type of fuel-cell, hydrogen is used as the “fuel” to directly generate electricity. With this type of fuel cell the only by-products are heat and water.
Having this technology on board of an aircraft is particularly attractive since it does not generate CO2, NOx, and potentially forms no contrails, or very limited ones. In order to use this advantage to its full extent we need an electric-powered aircraft, and therefore sufficient fuel cell capacity on board to generate enough power at an acceptable weight level.
‘Stacking’ fuel-cells for extra power
Because one single fuel cell is only a few millimetres thick and roughly the size of a letter envelope, it does not release much energy. Therefore, in order to realise sufficient power levels for use in an aircraft, hundreds of these fuel cells need to be electrically connected in series to form a “stack”. Subsequently, several such stacks are combined into multiple fuel cell “channels”. With this modular approach, the megawatt levels of power – which are needed for an electric aircraft – are achievable.
Partnering with automotive fuel-cell expert, Elring Klinger
While fuels cells themselves are already used in some automobiles, they do not fulfil the stringent requirements necessary for aeronautical use. Nevertheless, it made sense for Airbus to look towards the automotive industry for a prospective partner and provider, with whom to take fuels cells to the next level – to produce specially tailored fuel cell stacks and industrialise them for the aviation industry. The best partner it found was Elring Klinger, one of the leading providers of fuel cells in the automotive industry. In 2020, these two companies created a joint venture named “Aerostack”. Notably, Aerostack has also joined forces with other stakeholders, as well as those who are working on fuel-stack development as part of a German government supported project called H2Sky.
Understanding and tailoring fuels cells for aerospace use
Two years after Aerostack was formed, the collaborative work is well underway. The first prototype fuel cell stacks are already being evaluated by Airbus in Hamburg, where the teams are designing fuel cell systems, assembling and testing them.
“We are doing everything from scratch at quite an impressive speed,” enthuses Hauke Peer Lüdders, Head of Fuel-Cell propulsion systems for ZEROe Aircraft at Airbus. “We need to understand how fuel cell systems work and react. For that first step we are intentionally designing large ones to accommodate many sensors inside and allow us to analyse each equipment in the system, with good accessibility in order to tailor, test and fully understand the system behaviour,” he explains.
Design and testing the auxiliary system – an iterative process
Once the teams have tailored the entire fuel cell systems, it’s time to test them. First they need to make sure it is properly connected to the auxiliary system, the test bed, comprising hydrogen, nitrogen (for the tests only), coolant and air supplies – as well as a drainage outlet (for the derived water by-product). After the doors of the test bench are closed, the power is switched on and the process gets underway. Subsequently the teams can monitor – via special screens – the ongoing reaction, the production of by-products and of course the electrical power generated.
“We once experienced issues with the water management, so the drainage design is key,” notes Hauke. “It’s an iterative process, and it doesn’t always go the way we expected, so it brings useful learning opportunities which enable us to improve the process so that it becomes even more stable and robust.”
Hauke points out that what the teams are doing is also iterative in terms of the technology standards which Airbus and its partners are developing. “Even as these tests are progressing, the teams are also designing and developing the next-generation of fuel-cell stacks and systems. These will be more compact and more powerful, and which will lead to a version which can fly in Airbus’ planned ZEROe fuel-cell demonstrator.”
“In the end, it’s incredible what we have learnt in such a short timeframe! I couldn’t dream of a more exciting project to work on and I’m sure a lot in the team would say the same,” concludes Hauke.