Power-to-Liquids, explained
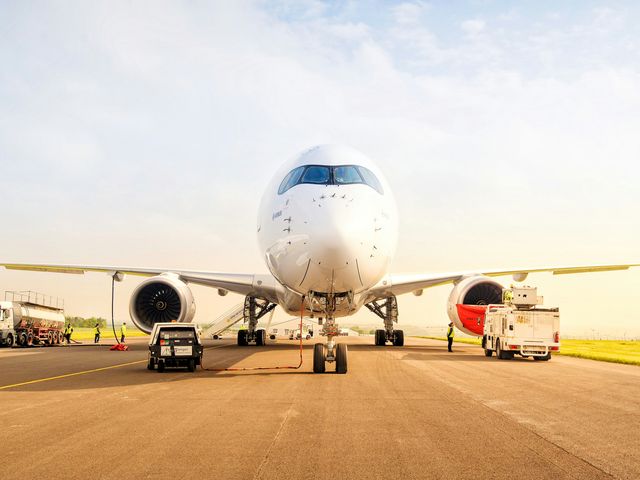
T
oday, the large-scale deployment of renewable energy is accelerating, as the world looks to increasingly decarbonise its energy mix. And a share of this renewable energy is expected to open up new possibilities, such as the conversion of renewable electricity into liquid fuels. Known as Power-to-Liquid (PtL), this type of sustainable aviation fuel (SAF) is emerging as an exciting option to fuel future aircraft.
In 1923, chemists Franz Fischer and Hans Tropsch decided to take a novel approach to converting coal into a new synthetic fuel – a process originally developed in Germany in 1913. Together, they tested an indirect way to liquefy coal in which solid coal is first transformed into a gas. The process involves introducing metal catalysts at temperatures of 150–300°C (302–572 °F) to set off a variety of chemical reactions resulting in liquid hydrocarbons – or a raw liquid form of carbon monoxide blended with hydrogen or water gas.
The process was such a success that coal-rich Germany used it during World War II to produce a replacement fuel for traditional fossil-based petroleum. In fact, 92% of Germany's air fuel and over 50% of its petroleum supply in the 1940s was created using the coal liquefaction process pioneered by Fischer and Tropsch.
A century later, the Fischer-Tropsch process is one of the main ASTM-approved methods for producing SAF. Today, this type of SAF is known as PtL, and it boasts improved combustion properties that could help significantly reduce emissions across a variety of sectors, including aviation.
One of the major advantages of PtL is that it can be transported and distributed via the existing network of fossil-fuel infrastructure, including pipelines and filling stations.
What is Power-to-Liquid or PtL?
PtL is a synthetically produced liquid hydrocarbon. Renewable electricity is the key energy source, and water and carbon dioxide (CO₂) are the main resources used in PtL production, which consists of three main steps:
- Renewable energy powers electrolysers to produce green hydrogen.
- Climate-neutral CO₂ – captured via, for example, Direct Air Carbon Capture – is converted into carbon feedstock.
- Carbon feedstocks are synthesised with green hydrogen – via processes such as Fischer-Tropsch – to generate liquid hydrocarbons. They are then converted to produce a synthetic equivalent to kerosene.
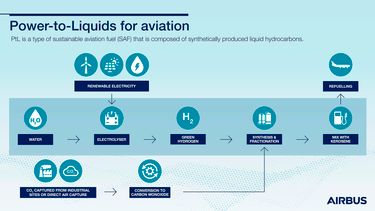
Capturing and storing CO₂ are central to the production of PtL. Indeed, recapturing the CO₂ released during combustion and combining it with hydrogen closes the loop in that the CO₂ that was initially released is reused to create fuel. For this reason, PtL’s “well-to-wheel” emissions – an important measurement that compares the efficiency of different solutions in relation to greenhouse gas emissions – can be reduced by as much as 90% compared to fossil fuels.
One of the major advantages of PtL is that it can be transported and distributed via the existing network of fossil-fuel infrastructure, including pipelines and filling stations. In addition, blending PtL with conventional kerosene (up to 50%) is already possible, according to current jet fuel standards.
However, today’s PtL is currently produced at a relatively high cost and on a low scale. This is expected to change as the green hydrogen ecosystem continues to ramp up worldwide. Experts predict that PtL could be ready to use on a wider scale between 2025 and 2030.
Partnering to develop PtL at a large scale
PtL is an alternative fuel that is JetA/JetA1-approved. It offers the required energy density, a prerequisite for fuelling transport modes that require a high power demand to travel long distances. This makes PtL an interesting solution to fuel aviation – and Airbus is taking notice.
In fact, Airbus sees PtL as having huge potential, not only in terms of climate impact, but also in cost and scalability. This is why Airbus is partnering with the SAF+ Consortium, the first organisation in North America to target wide-scale PtL production.
The objective of the partnership is to provide Canada – and eventually the rest of North America – with a sustainable supply of PtL to enable low-carbon flying. The demonstration plant, located near Montréal, will start production in 2021, with large-scale industrial production expected by 2025.