This rocket propellant fuelled the 1981 Space Shuttle
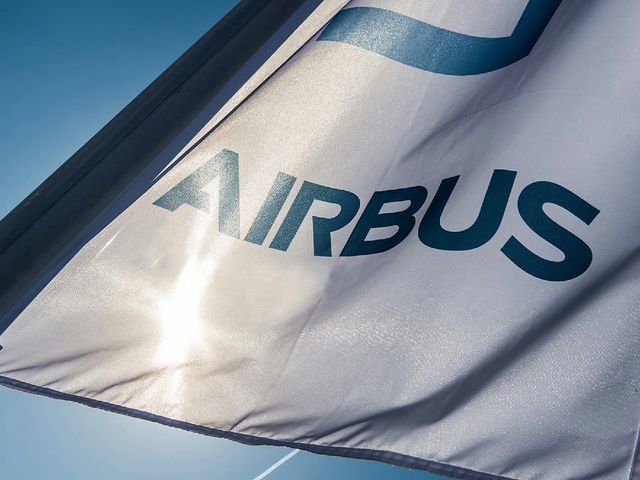
2021 marks the 40th anniversary of the STS-1 Space Shuttle launch. Integrated in the main external tank, liquid hydrogen was successfully used as rocket propellant on a crewed spacecraft. As the urgency to decarbonise intensifies, the aviation industry is looking to leverage the lessons learned on liquid hydrogen from the space industry to apply them to future zero-emission aircraft.
The day was April 12, 1981. At the Kennedy Space Centre in Florida, USA, the launch control crew was abuzz: in only a few short minutes, the world’s first space-rated orbiter would officially launch and hurtle towards outer space.
This was history in the making.
And then it happened: at 12:00:03 (local time), the STS-1 Space Shuttle—a spacecraft nearly ten years in development—lifted off from the launch pad in a cloud of steam and smoke as the control crew watched from afar with bated breath. A few minutes later, two reusable solid rocket boosters and a disposable external tank filled with liquid hydrogen detached from the orbiter. And several minutes after that, the orbiter pierced through the Earth’s atmosphere to reach orbit. Cheers, applause and even a few tears filled the launch control centre. The crew may not have known it back then, but this was the start of one of the most successful space shuttle programmes ever.
Forty years later, the technologies used to launch the space shuttle are still as relevant as ever. In fact, the use of liquid hydrogen as a powerful rocket propellant remains one of the most significant technical accomplishments of 20th-century rocketry. In addition to NASA’s various space programmes, the European Space Agency (ESA) also used liquid hydrogen for the Ariane rocket in the 1970s.
Today, liquid hydrogen continues to be the signature fuel of space exploration. Tomorrow, it could be used in new ways—such as fuelling a future zero-emission commercial aircraft.
We want to bring all of the benefits of liquid hydrogen as a powerful and green propellant to the aviation industry.
Renato Bellarosa, Head of Space Programmes at Airbus Italia
The world’s most powerful rocket propellant
Hydrogen is an extremely powerful rocket propellant: it has the lowest molecular weight of any known substance and burns with extreme intensity (5,500°F). And when combined with an oxidiser such as liquid oxygen, liquid hydrogen boasts the highest efficiency—relative to the amount of propellant consumed—of any known rocket propellant.
A major component of the STS-1 Space Shuttle launch vehicle was the disposable external tank containing liquid hydrogen fuel and liquid oxygen oxidiser. This tank acted as the “backbone” of the space shuttle and supplied the fuel and oxidiser to the orbiter’s three main engines during lift-off and ascent.
But preparing liquid hydrogen for use as a rocket propellant has been no easy feat. Oxygen and hydrogen can be liquefied only at extremely low temperatures—which poses enormous technical challenges. These include the following:
- Cooling systems, which take space and can be heavy, are required at all times to ensure liquid hydrogen can be stored.
- To keep from evaporating, liquid hydrogen must be insulated from other heat sources, such as rocket engine exhaust and air friction during flight.
- Liquid hydrogen expands rapidly after absorbing heat, therefore venting is required to prevent tank explosion.
- Liquid hydrogen is extremely lightweight and can leak through tiny pores in welded seams.
- The extreme cold needed for liquid hydrogen can render metals brittle and weaken welded seams.
The space industry has spent decades developing the technical expertise needed to address these challenges. And it has been successful in doing so—a know-how that will be vital to helping the aviation industry solve the challenges of using liquid hydrogen in future aircraft.
Liquid hydrogen for the aviation industry
Liquid hydrogen, compared to gaseous hydrogen, is increasingly emerging as the most promising option for hydrogen storage on aircraft. This is because liquid hydrogen is typically used as a concentrated form of hydrogen. Like most gases, hydrogen stored as a liquid takes less space than when stored as a gas at normal temperature and pressure. However, to reach a fully liquid state at atmospheric pressure, hydrogen must be cooled to 20.28 Kelvin (−252.87 °C). This is why cryogenic tanks play a crucial role in hydrogen transport and storage for future aircraft propulsion systems.
Engineers from Airbus Defence and Space are working to support the ZEROe project team in the development and industrialisation of cryogenic tanks for liquid hydrogen storage.
As part of the three-year collaboration, the teams are looking into the following aspects:
- Identifying trade-offs to determine the best approach to storing liquid hydrogen on aircraft (i.e. composite vs. monolithic tanks)
- Optimising the design of liquid hydrogen pressure vessels, including critical thermal aspects
- Testing damage tolerance, fracture control and non-destructive inspections
- Analysing advanced manufacturing and industrialisation techniques
- Defining and supporting testing activities for liquid hydrogen storage systems
“We want to bring all of the benefits of liquid hydrogen as a powerful and green propellant to the aviation industry,” explains Renato Bellarosa, Head of Space Programmes at Airbus Italia. “But to do so, we need to use due diligence to make sure the cryogenic tanks meet our rigorous safety standards. This is at the heart of our work today.”