Clever connections
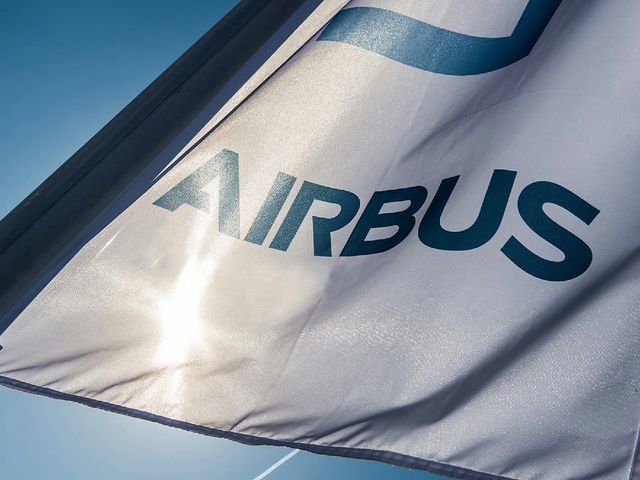
Intelligent mousetraps or app-controlled shoes are distracting us from the real potential of the Internet of Things. The IoT is set to change the world. Airbus engineers want to help shape this transformation and are laying the foundations for an interconnected revolution in manufacturing.
Earlier in 2017, a British engineer and his supposedly ‘intelligent’ kettle proved the source of much online amusement. It all started at 9 am, when the man wanted to use his new Wi-Fi kettle to make a cup of tea. He first attempted to connect the device to his smart speaker, but the kettle had other ideas: it didn’t have the right software.
As the day progressed, the Briton encountered one problem after another, so he decided to tweet about his battle with the smart kitchen device – for 11 hours. That’s how long he had to wait to enjoy his first cup of tea.
The Internet of Things
Stories like these don’t do much to enhance the image of the Internet of Things (IoT). Some critics say inventions like Wi-Fi kettles, intelligent mousetraps or app-controlled shoes show that the hype surrounding IoT is unjustified and it causes more problems than it solves.
It’s an unfair accusation, says Janos Sztipanovits, Director of the Institute for Software Integrated Systems at Vanderbilt University in Nashville, Tennessee. “There are things that we interconnect just because we can, not because we need them. But there’s a huge difference between that and building something so you can depend on it. Look at smart medical devices, vehicles or connected homes – there are a massive number of applications that are extremely useful.” Particularly promising is intelligent networking within the industrial sector, known as the Industrial Internet of Things (IIoT).
A 2015 study by McKinsey came to the same conclusion. It estimates the IoT could have a global economic impact of up to €10.4 trillion per year by 2025. With a possible impact of up to €3.5 trillion, manufacturing represents the sector with the most potential.
The IIoT is the connection of critical machines, devices and sensors to communications software across high-stake industries such as aerospace and defence. The resulting system can monitor, collect, exchange, analyse and preventively act on information to intelligently change and adapt itself. Airbus sees a future where the intersection of people, data and intelligent machines will have far-reaching positive impacts on the productivity, efficiency and operations of its shop floors.
The interconnection of human, machine and product along the entire value chain can bring massive gains in efficiency and an ideal use of resources. Each part can think for itself. Networked conveyor belts, for example, decrease their speed to match the workload, thus reducing energy consumption and wear and tear. Tools know what task they need to do next and warehouses automatically order more material when it’s needed.
What for non-experts might sound simple is actually an immense undertaking. Realising the enormous potential of the IIoT requires a lot more than simply installing a mass of sensors in factories: it requires intelligent tools, uniform standards and open platforms. Otherwise, the same problems arise as with the intelligent kettle: the device itself may be smart, but it cannot be integrated into its surrounding environment.
Intelligent tools
That’s why, seven years ago, Airbus began to develop an open platform project coined CITAR: Collaborative Intelligent Technologies for Automated Routines. Forming the basis for this software–hardware platform are intelligent tools that communicate with each other. To make themselves understood, they have to speak the same language.
That means when Airbus orders a robot, it must be capable of more than just drilling, for example: it has to be able to flexibly integrate itself into the company’s ecosystem and take on other tasks: “even those that we hadn’t thought of when we ordered the robot,” adds Sébastien Boria, Robotics and mechatronics leader at Airbus.
“To reach this level of compatibility and openness, we give smart device manufacturers a starter kit outlining requirements they must fulfil.” For example, manufacturers would have to use microchips that Airbus has already tested together with the chip producers. The benefits of such an approach go way beyond Airbus: the clearer the instructions and the more open the collaboration, the more efficiently suppliers can work, saving them time and money.
Machine learning
Interconnected production and data gathering is only the first step, however. It doesn’t matter how much data you have if you can’t interpret it correctly and use it in the right context. The CITAR project enables precisely this: data is continuously received from and injected into running manufacturing processes. This allows the integrated system not only to react to event triggers and commands but also to learn and adapt how it operates. The basis for this is formed by machine learning and artificial intelligence (AI).
What CITAR has set out to do will immediately help our workers, but what it will unlock is even more amazing.
With machine learning, it is possible to learn about how to optimise existing processes. Cognitive computing and natural language processing make it possible to extract knowledge from the massive amount of engineering and manufacturing documents to create adaptive work processes.
“With CITAR, we can go even further and close the loop such that we apply situational awareness and, for the first time, truly learn in real-time as work orders are processed. This is a step change for AI in manufacturing,” says Ronny Fehling, Data-driven technologies VP.
A new chapter in manufacturing
To get the view of an external expert, Airbus asked Janos Sztipanovits to audit CITAR. As Vanderbilt University’s representative in the Industrial Internet Consortium (IIC), he is well versed in the latest technologies for IIoT platforms. A total of 250 companies, research bodies and universities make up the IIC, which aims to promote accelerated growth in the IIoT. According to Sztipanovits, CITAR currently represents the absolute cutting edge in this area.
"It’s the new gold rush for large IT companies. The likes of Intel, Microsoft and Google are all working to create new platforms and solutions", added Sztipanovits.
What is clear is that manufacturers are at a crossroads and it is no longer possible to ignore this shift. The leaps forward in AI, interconnected systems and IoT platforms are driving the next industrial revolution, and these platforms are becoming the new marketplace battleground.
Curtis Carson, head of manufacturing digitalisation at Airbus, also talks of a monumental opportunity for the company: “Our industry is only just beginning to adopt IIoT. We are now working to shape this trend.”
Having already partially implemented the CITAR platform, the plan is to now accelerate this adoption and encourage greater collaboration. With such an open platform, Airbus and its partners can set standards for the aerospace industry.
Carson likens it to the early days of the Android operating system. It was actually devised for use with digital cameras, before going on to establish itself as an open operating system for mobile devices. Today, it dominates the market and can be found in 90% of smartphones.
“This is what’s at stake here,” says Carson. “The time is now to take the lead and define the rules ourselves to write the next chapter of manufacturing: the story of exponentially smarter, hyper-collaborative factories.”
Beata Cece