4D printing and digital materials
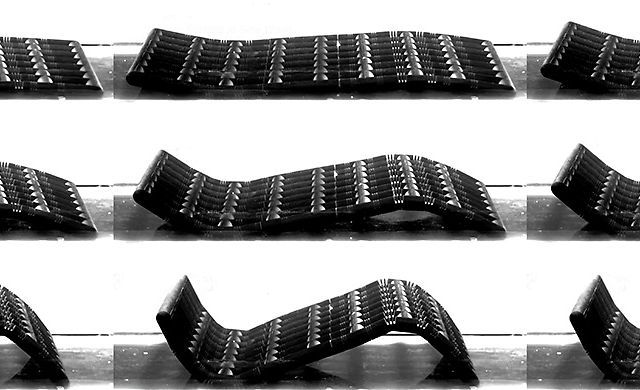
4D printing: the extra dimension
Airbus is aiming to revolutionise the aerospace industry with a new generation of intelligent materials, partnering with some of the world’s leading researchers.
4D printing: the extra dimension
Cutting-edge technology doesn’t always imply greater complexity. At least that’s what Skylar Tibbits thinks. The Research Scientist at the Massachussets Institute of Technology (MIT) Department of Architecture is pioneering work on so-called '4D printing', creating dynamic 3D printed materials that can change shape by themselves when confronted with outside forces such as water, movement or a change in temperature.
Shape-shifters
The technique has potential for a wide range of uses, including the aerospace sector, and Tibbits is collaborating with Airbus to develop a special air inlet component.
Today’s nacelle ventilation air inlets are static, so the air flowing through them varies greatly according to the speed of the aircraft. At cruise condition, air flow is much greater, which can adversely affect fuel consumption.
This collaboration with Airbus was born around the company's ProtoSpace facilities, where researchers and engineers develop disruptive concepts and accelerate the pace of innovation.
Thanks to programmable carbon fibre, the new air inlet would adjust itself automatically to control air flow used to cool the engine. This would remove the need for the heavy mechanical system currently performing this task.
‘Responsive’ objects
Airbus has already successfully tested the inlet in a wind tunnel, and the potential is clear, as Christophe Cros, from Airbus’ Emerging Technology and Concept team explains. “Air vehicles have lots of air inlets for ventilation or thermal control that could benefit from this technology. We could also envisage extending the application to movable surfaces or even aircraft cabins to mediate pressure or make them more breathable.”
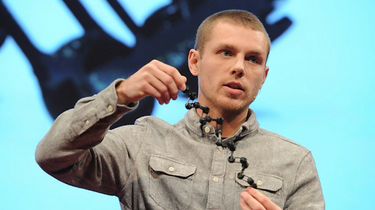
"4D printing is really all about simplicity, removing components, extra weight and control systems"
Skylar Tibbits
Director of MIT's Self-Assembly Lab
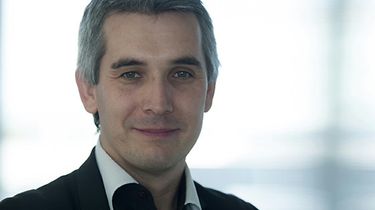
"4D printing provides the potential to create products that adapt to us and our environment"
Airbus' innovator Christophe Cros
Digital fabrication – Developing 'industrial Lego'
Together with MIT, Airbus is exploring the use of digital manufacturing in aerospace. This disruptive approach echoes the body's construction of proteins from amino acids to build complex structures.
Digital aerospace structures
While many others are focusing on 3D printing, Neil Gershenfeld has dedicated his research to something called digital fabrication. “It will allow individuals to design and produce tangible objects on demand, wherever and whenever they need them,” claims the Director of MIT's Center for Bits and Atoms.
On an industrial scale, he compares it to “carbon-fibre Lego” that will help reduce mass and save weight. “Parts will join like snap-together building blocks to give a structure that is lightweight, extremely durable and easy to assemble and reassemble.”
Airbus’ collaboration with MIT
Airbus has signed a deal with MIT to work with Gershefeld on exploring the use of digital fabrication in aerospace. “Currently, everything is so big – you need huge tools to produce large parts and then transport them for assembly,” he says.
“Digital materials could use smaller, interlocking pieces. Rather than building large, monolithic, single-use components, we turn the materials into simple, repeating, functional bits.”
4D printing at MIT: Self-assembling components
The expanding materials were placed strategically on the main structure to produce joints that stretched and folded like a bendy straw when activated by water, forming a broad range of shapes.
In the future, the technique is expected to produce larger structures which can handle more complex transformations, as well as smaller, miniaturised models that can be used in an aircraft's body.
Other successful stimuli used to change shapes are electroactive polymers, pressurised fluids or gasses, chemical stimulus and even light.
Pictures courtesy of MIT
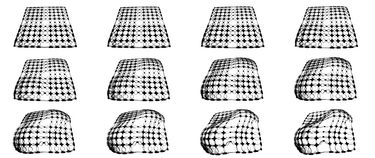
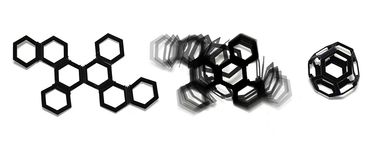
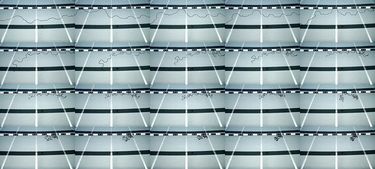