H225 FCOM: making a mark on operations at NHV Norway
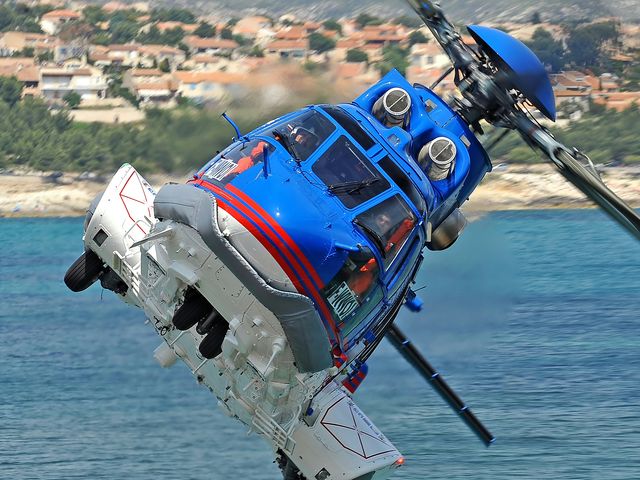
Summary
- The H225 flight crew operations manual (FCOM) was published a year ago by Airbus Helicopters for H225 helicopters operating offshore, to give operational recommendations in the use of automation technology. A year later, we take a look at how the document is changing daily operations at the Norwegian brand of NHV, with accountable manager Dag Johan Saetre, and flight operations manager Bram Sevenhuijsen.
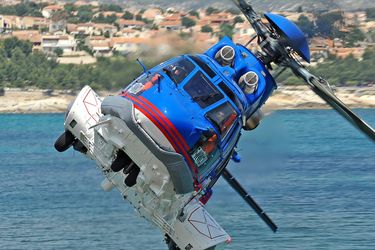
Dag Johan Saetre: We started using the FCOM in September. We cooperated with Airbus Helicopters in Aberdeen to start implementing the FCOM in our flight operations procedure.
Bram Sevenhuijsen: We hired one of the instructors from Aberdeen as a contractor, to fly the line and get to know how we operate. It became very much a working process, of how we should adopt these recommendations.
D.J.S.: Our whole operations manual has been changed. The FCOM is aimed at the people writing the operations procedures. They received the FCOM and adopted these recommendations into the company’s operating procedures.
B.S.: We sent the procedures to our pilots when they got their FCOM-specific training in the simulator. And we’ve gone further. We’ve done an evaluation round, and now we’re sending the crews on a second round to the sim.
D.J.S.: When the pilots started training using the FCOM, they were amazed by the extra features built into the aircraft, which they never used.
B.S.: One thing is how precise the automation is in supporting, for instance, the profiles we fly when you have an engine out. We were trained to do it manually. You always wanted to be gentle with the one remaining engine, so you didn’t milk it as much as the autopilot is able to. The autopilot is really able to get all of the available power out of it, and increase safety that way.
D.J.S.: Until now, much of our flight operations procedure was built on how pilots and instructors know the aircraft, and not on how Airbus Helicopters really designed the helicopter and all the possibilities built into it.
B.S.: One of the best elements is the go-around feature. We’re using it pretty much on every takeoff now. We thought the go-around button would only work when all engines were up. But the biggest benefit for us is actually if we do lose an engine or go into an abnormal situation. The autopilot executes the profile at its most efficient, so the chances of a pilot error are greatly reduced. It alleviates a lot of the work pressure, and enables the pilot to assess the situation much better. This is definitely my favorite discovery.
D.J.S.: The pilot can focus outward more, to see what’s happening around him, and to monitor other parts of the aircraft instead of trying to control the engine and flight controls.
B.S.: We have low-visibility departure procedures. We need to have 150 meters visibility and a 50-foot cloud base so that at TDP (takeoff decision point), you have enough visual reference in case you need to make a rejected takeoff. But if you continue the takeoff and go straight into IMC (Instrument Meteorological Conditions) at 50 feet, then the autopilot really supports the pilot in achieving the necessary speeds for the climb-out, especially in abnormal situations (engine malfunctions, etc.).
D.J.S.: I’ve only had positive feedback. People have seen the advantages of the FCOM. They’ve noticed less workload in the cockpit.
B.S.: The buffers for safety have increased. In the past the procedure in an abnormal situation was for the pilot flying to focus on handling the collective and cyclic and pedals to maintain a safe flight path. Now he can have the autopilot take over part of that job. It reduces the pressure on the pilot flying, which is a big benefit for safety.
D.J.S.: I see this as the next step in safety, to start using the aircraft the way it was designed by Airbus Helicopters to be used.
B.S.: The FCOM is not only a help in the use of automation. For me, it’s the awareness of extra safety features.