Hydrogen combustion, explained
How hydrogen’s unique properties are ideal for engine combustion
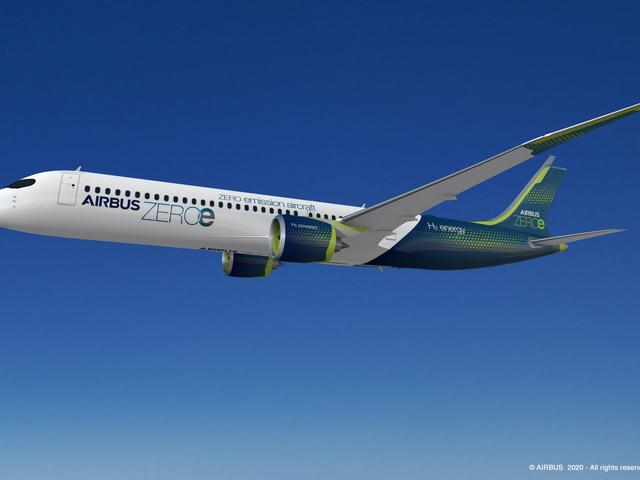
Today’s internal combustion engines in aircraft can be modified to run on alternative fuels for improved environmental performance. Now, hydrogen combustion—either via gas or liquid—is emerging as one of the most promising options in this respect. Airbus is exploring the technology’s potential in preparation for its zero-emission aircraft programme.
When the world’s first internal combustion engine revved up, it was hydrogen gas—not gasoline or diesel—that burned as its fuel.
The year was 1804. After successfully designing several steam-powered carriages, Franco-Swiss inventor Isaac de Rivaz set his sights on using an explosive charge—instead of steam—inside a stationary engine to power a pump. His first experiments focused on creating an explosion within the engine’s cylinder to drive the piston out. At the time, he used a mixture of hydrogen and oxygen gases to ignite this explosion—and it worked. By 1807, de Rivaz’s experimental prototype engine was being used to propel a carriage a short distance—thereby garnering the distinction as the world’s first vehicle driven by an internal combustion engine.
Throughout the 20th century, automobile companies, universities, inventors and hobbyists alike further tested the viability of internal combustion engines powered by hydrogen. In fact, in 1970, inventor Paul Dieges was the first to patent a modification to gas-powered internal combustion engines, which enabled them to run on hydrogen.
Today, hydrogen combustion engines have proven their ability to successfully power a variety of vehicles, from cars to buses. Tomorrow, hydrogen combustion may just power future commercial aircraft.
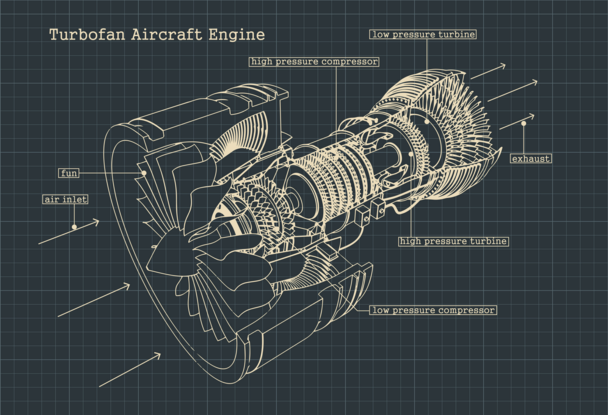
Hydrogen combustion: how does it work?
Combustion, or burning, is a chemical process that involves releasing energy from a fuel and air mixture. In the case of hydrogen combustion, liquid or gaseous hydrogen is burned in a modified gas-turbine engine to generate thrust. This process is identical to traditional internal combustion, except hydrogen replaces its fossil fuel counterpart.
Consisting of a fixed cylinder and one or more moving pistons, a spark ignition engine works in the following way:
- During the intake process, fuel is mixed with air and introduced into the cylinder.
- The piston then compresses the fuel-air mixture, which is ignited by a spark. Ignition results in combustion.
- The expanding combustion gases drive the piston, which rotates the crankshaft.
- This rotational motion turns the wheels, in the case of automobiles.
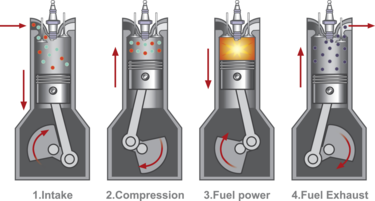
The only way to determine which hydrogen technology is best-placed to fuel our ZEROe concept aircraft is to test, test, test.
Matthieu Thomas, ZEROe Aircraft Lead Architect
Hydrogen has many unique properties that make it suitable for combustion, including the following:
- Wide flammability range: Hydrogen can be combusted via a wide range of fuel-air mixtures. In fact, hydrogen can run on a “lean” mixture, which means the amount of fuel is less than the amount needed for combustion with a given amount of air. This results in greater fuel economy and a final combustion temperature that is generally lower, which reduces the amount of pollutants, such as NOx, emitted via the exhaust.
- High auto-ignition temperature: Hydrogen’s high auto-ignition temperature enables higher compression ratios in a hydrogen engine compared to a hydrocarbon engine. A higher compression ratio results in greater thermal efficiency, or less energy loss during combustion.
Putting hydrogen combustion technology to the test
Hydrogen combustion has already been used to fuel aircraft. In fact, in 1988, the world’s first experimental commercial aircraft operating on liquid hydrogen (and later, liquefied natural gas) took to the skies: the Tupolev Tu-155. It flew approximately 100 test flights and was then placed into storage.
Now, more than 30 years later, the aviation industry is once again turning its attention to hydrogen combustion in commercial aircraft. Indeed, Airbus’ ZEROe concept aircraft could run on hydrogen combustion. To explore the possibilities and limitations of this technology for commercial aircraft, Airbus will team up with a variety of partners across industries.
“The only way to determine which hydrogen technology is best-placed to fuel our ZEROe concept aircraft is to test, test, test,” says Matthieu Thomas, ZEROe Aircraft Lead Architect. “We look forward to sharing more details about an exciting cross-industry partnership on hydrogen combustion.”
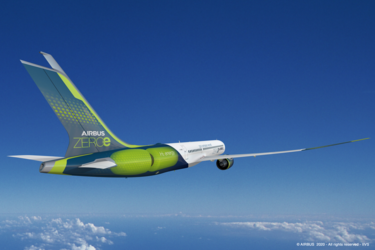
But for hydrogen combustion to work, liquid hydrogen must be stored safely and securely on board aircraft. Due to hydrogen’s unique properties, this can be tricky. For example, tanks need to be insulated to avoid evaporation if heat is carried over into the stored content by factors such as conduction. This is why the Airbus Defence and Space’s Engineering Division has stepped in to help. The team will provide support for the development and industrialisation of cryogenic tanks for liquid hydrogen storage in a three-year project collaboration with the ZEROe programme team.
“The space industry has been using pressure vessels for the storage of liquid propellant to fuel space exploration for decades,” explains Renato Bellarosa, Head of Propulsion Products and Tanks at Airbus Defence and Space. “So we have a lot of expertise in damage tolerance, in advanced manufacturing technologies and in vessel pressure testing, all of which is key to supporting the development of liquid hydrogen storage tanks for future aircraft propulsion systems. It’s cross-industry collaboration like this that will bring us closer to putting a hydrogen-powered aircraft into the skies over the next decade.”
Get the latest innovation news
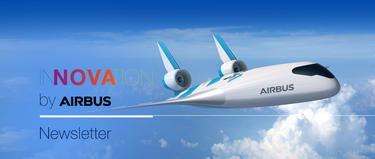
See more Innovation news
Continue Reading
Powering production and protecting people with exoskeletons
Web Story
Innovation
Discover how Airbus is revolutionising aircraft production with industrial exoskeletons that improve ergonomics and safety for workers.Airbus and MTU Aero Engines advance on hydrogen fuel cell technology for aviation
Press Release
Innovation
Airbus and Critical Software explore strategic partnership in embedded software…
Press Release
Innovation
Strengthening Europe's sovereignty: Airbus and Quantum Systems work on ecosystem for…
Press Release
Defence
Airbus at Paris Air Lab 2025: Discover Tomorrow, Today
Web Story
Innovation