At Airbus we believe hybrid-electric power can reduce aircraft CO2 emissions by up to 5%. That figure could be as high as 10% for helicopters, generally lighter than fixed-wing aircraft. Hybridisation is a big step in the aerospace sector's decarbonisation journey and Airbus is leading a cross-industry effort to make it happen.
Decarbonising flight requires a range of disruptive solutions that mix new fuel types and fledgling technologies. One such solution, hybrid-electric propulsion can improve the energy efficiency of every aircraft class.
Exploring electrical power
Helicopters are blazing the trail. Airbus has already flight tested a hybrid-electric system which takes over from the thermal engine should it fail. The Engine Back-up System is the forerunner of larger hybrid propulsion systems that will be tested at a later stage, using a demonstrator rotorcraft.
Also under development, Ecopulse is the fruit of collaboration between Airbus, Daher and Safran. This demonstrator is based on a light aircraft. It’s helping us increase our knowledge of distributed propulsion systems and multiple power source management. Ecopulse uses an innovative lightweight, compact high voltage Lithium-Ion battery developed by Airbus Defence and Space.
Of course medium-sized commercial and military aircraft will require much more electrical power, up to one megawatt of onboard-generated energy. That energy can be used to power some systems and relieve the main engine during operations such as push-back and take-off.
However, reaching the <5% target requires Airbus and engine manufacturers to jointly develop a new, more efficient class of gas turbine. To this end Airbus has already initiated a number of projects to demonstrate different hybrid engine concepts with different power levels. Deciding which electric motor type will support them is equally important.
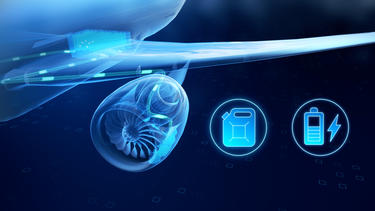
Selecting an electric motor
Electric motors convert electrical energy into mechanical energy; generators perform the opposite operation. There are several types of electric motor, but the main characteristics of interest for hybridisation are their power-to-weight ratio and relative efficiency. At current levels, a reasonable power-to-weight ratio is 6-8 kW/kg, but it is unsuited to weight-limited applications. Happily these figures are likely to double in the next ten years.
Given the relatively few moving parts they contain, electric motors are easier to service and less exposed to failure than gas turbines. They can also operate at a lower temperature range, removing the warm-up phase gas turbines need.
The electric motor sits within a functional aircraft ‘architecture’. For hybrid-electric aircraft, the choice is between two architecture options: serial and parallel.
Serial or parallel architecture?
In a serial architecture, a single mechanical power source drives the propeller or fan. Batteries aren’t the only power source. There are alternatives, including hydrogen fuel cells. In any case, the propeller is always driven by an electric motor, enabling distributed propulsion.
As far as hybridisation is concerned, this is serial architecture’s biggest advantage. But it means adding weight in the shape of a generator, to convert mechanical power to electrical power.
In a parallel architecture, the gas turbine sometimes operates below peak efficiency. However, a smaller and lighter electric motor is enough to meet requirements. So a parallel architecture is better suited to hybrid applications. What about the battery that powers the electric motor sitting within it?
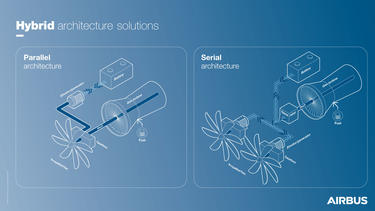
Battery breakthroughs
The main shortcoming of current-generation batteries is their low energy density compared to kerosene and hydrogen. For instance, the density of Lithium-Ion (Li-Ion) batteries widely used by the automotive sector reaches around 200 Watt-hours per kilogramme (Wh/kg). By comparison, kerosene’s energy density is some 50 times higher. Even if numerous studies argue that Li-Ion has further room for improvement, aircraft electrification needs something altogether more powerful.
Airbus is working alongside players in other sectors to get there. “There are common challenges and shared areas of interest,” says electrical generation systems expert Leire Segura, citing battery size, charging and cooling. “We’re learning together.”
A compromise has to be found between performance, volume and mass in an aircraft’s weight-sensitive, aerodynamically-optimised environment. “We’re looking at technologies already deployed in the automotive sector, which drives the market,” says Segura. Li-Ion is a big step forward, already delivering significant performance gains compared to Nickel-Cadmium. Yet the Airbus expert doesn’t expect a Li-Ion eureka moment any time soon.
“The holy-grail is the solid-state battery,” Segura enthuses. Solid-state provides solutions to many Li-Ion drawbacks. But as mentioned, aircraft certification requires bespoke design. Airbus is in discussions with a number of aerospace suppliers who provide electrical systems. “We’re at the definition phase, all upskilling at the same time,” she notes. “Realistically, we don’t expect to see prototype solid-state batteries that are adapted for aerospace before 2030.”
Unlike the liquid electrolytes found in Li-Ion batteries, ‘solid’ electrolytes mitigate the risk of thermal runaway (overheating). The risk remains but the consequences are far less severe, making it easier to design a safe battery system.
Solid-state is an enabler. High-performance battery technologies like lithium metal have been around for over 40 years, but the risk of runaway due to their instability is too high. Solid electrolytes cancel out that risk, opening the way to improved performance. Mitigating thermal runaway also makes the battery design simpler. Fewer parts are needed to ‘dress’ its cells. This has a positive weight impact.
Charging options
Whatever the technology, batteries need to be charged. For commercial aviation there are three options: swapping depleted units for new ones on the ground; or installing charge points at the gate, potentially using renewable energy. The latter requires investment in infrastructure but in the long term this would be offset by fuel savings.
Thirdly, where ground infrastructure is lacking, the aircraft’s engines could recharge the batteries during the cruise phase of a flight. “The reality could well be a mix of all three,” says Segura, “depending on individual airline and airport choices.”
Joining forces for faster results
It's already clear that a collaborative approach will deliver the fastest results in terms of battery maturity and integration. To that end, Airbus and Renault Group announced a partnership agreement at the Airbus Summit in November 2022.
The two companies are joining forces to advance research into energy storage and management. Both are crucial technologies not only for hybridisation, but the entire transport sector’s long-term sustainability. Decarbonisation is nothing if not a collective endeavour.
Airbus is taking a ‘modular’ approach to hybridisation. Karim Mokaddem, Airbus’ head of electrification, explains:
A module is a set of technology building blocks. They have a common voltage network, common interfaces and share control of an electric motor’s speed, torque and power. Some modules can be used for every hybrid-electric solution we are studying; some are specific to each project.”
Discover more Innovation news
Continue Reading
Web Story Innovation
Powering production and protecting people with exoskeletons
Discover how Airbus is revolutionising aircraft production with industrial exoskeletons that improve ergonomics and safety for workers.Press Release Innovation
Airbus and MTU Aero Engines advance on hydrogen fuel cell technology for aviation
Press Release Innovation
Airbus and Critical Software explore strategic partnership in embedded software…
Press Release Defence
Strengthening Europe's sovereignty: Airbus and Quantum Systems work on ecosystem for…
Web Story Innovation
Airbus at Paris Air Lab 2025: Discover Tomorrow, Today