Large-scale 3D printing goes to space on Airbus’ Eurostar Neo satellites
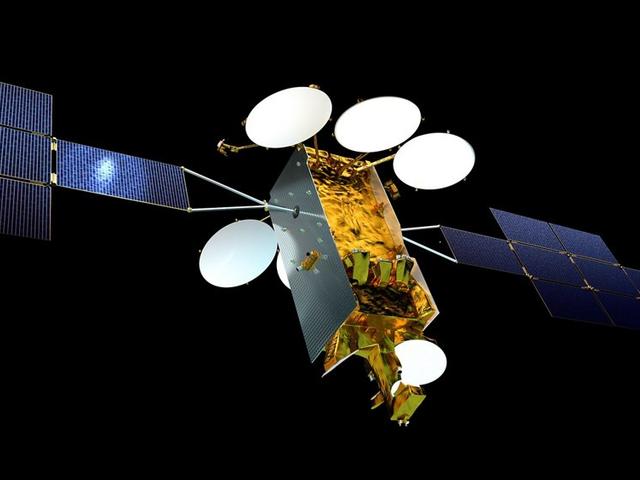
Radio frequency components are at the heart of every telecommunications satellite, and such parts are now being produced by Airbus in large volumes with innovative Additive Layer Manufacturing (ALM) technology – also known as 3D printing – for its latest spacecraft: the Eurostar Neo-series relay platform.
A total of 500 radio frequency (RF) components, composed of multi-waveguide blocks and switch assembly networks, have been 3D manufactured by Airbus Defence and Space in Portsmouth, UK for two Eurostar Neo spacecraft that will join the in-orbit fleet of Eutelsat, a major provider of satellite communications services.
Efficient production using ALM
These two satellites are called EUTELSAT HOTBIRD 13F and 13G. They will reinforce and enhance Eutelsat’s TV broadcasting services over Europe, the Middle East, and North Africa.
Using 3D printing for the EUTELSAT HOTBIRD satellites provides major labour savings during assembly enabling our teams to focus on more value-added tasks, as well as a significant reduction in the number of individual parts.
This is recognised as the first large-scale deployment of RF products using the ALM process, and it puts us in an industry-leading position for the technology’s application in producing radio frequency components.
- Gareth Penlington, HOTBIRD Payload Manager
Airbus’ manufacturing team in Portsmouth developed innovative designs for the Eurostar Neo’s multi-waveguide blocks and switch assembly networks to be 3D printed, taking them from initial concept and patenting through industrialisation and the completion of a successful qualification programme.
“This is recognised as the first large-scale deployment of RF products using the ALM process, and it puts us in an industry-leading position for the technology’s application in producing radio frequency components,” Penlington said.
The no. 1 EUTELSAT HOTBIRD satellite’s communications module was transferred earlier this month from Portsmouth to the Airbus Defence and Space facility in Toulouse, France, where the spacecraft’s full build-up will be completed. Assembly of the second HOTBIRD communications module is now underway in Portsmouth, with its testing to begin in February.
Q&A
Is it correct that all 500 additively manufactured components are also all integrated into the satellites (i.e. around 250 per satellite)?
Yes – there are number of different components and designs on both spacecraft.
What do the components look like and how big are they – size, weight, etc?
There are more than 100 different waveguide designs along with other network designs. (Waveguides route the RF signals around the spacecraft.) The size of the components range in size from about 300mm to about 100mm.
What additive manufacturing technology (e.g. selective laser melting) and what material were the individual components made of?
Material is aluminium silicon magnesium (AlSi10Mg) and yes uses SLM selective laser melting
What were the particular challenges of additive manufacturing compared to conventional manufacturing?
Waveguides need to have a smooth surface to achieve the required RF performance, and the ALM components require post processing to achieve this.
Can the advantages of additively manufactured components also be quantified?
We have achieved considerable schedule reductions over existing conventional waveguides. On average we have halved the production time of wave guides using ALM.
Approximately how long is the development time until an additively manufactured satellite component flies into space?
Initial work on ALM components to first took just over two years, but now that processes have been industrialised it is only a matter of months.
Does Airbus manufacture these components itself or via service providers and how is quality assurance and certification carried out here (possibly analogous to the TRLs on aircraft construction)?
We used third party suppliers who underwent full supplier and qualification processes.
Who decides which components in the satellite are additively manufactured (Eutelsat or Airbus) and what criteria are used as a basis?
Decisions are taken by Airbus but always with customer approval. The overall aim is to be improve schedule.
And how do you assess the importance of additive manufacturing currently and in the coming years?
Additive manufacturing is vitally important and the technology is now available as a baseline for the payload customization teams to utilize. We envisage further schedule improvements and reduced cost of manufacture and assembly in the future using this technology. On average an ALM item replaces a part which had five separate components.
Discover more Space news
Continue Reading
Glaciers in danger: satellites underscore extent of climate emergency
Web Story
Space
Satellites help scientists like Heïdi Sevestre track rapid glacier melt. Discover the impact of their changes on Earth’s life & ecosystems.Airbus awarded Hisdesat contract to build PAZ-2 satellites reinforcing Spain's…
Press Release
Space
Airbus Defence and Space implements new organisation to shape division’s future…
Press Release
Company
Why you should care about space weather
Web Story
Space
Biomass, a satellite to look inside the world’s forests like never before
Web Story
Space