· New standard in digitalisation and automation, driving efficiency
· Key enabler in Airbus’ single-aisle ramp-up
Airbus has inaugurated the fourth Hamburg, Germany A320 Family production line. Making use of digital technologies and a more flexible industrial setup, the innovative state-of-the-art line is a key enabler for ramping up the single-aisle programme to 60 aircraft per month by mid-2019.
Frank Horch, Hamburg’s Senator of Economy, Transport and Innovation and Thomas Jarzombek, Federal Government Coordinator of German Aerospace Policy, witnessed the milestone together with Guillaume Faury, President Airbus Commercial Aircraft, and 500 distinguished guests at a special ceremony in Hamburg.
“The inauguration of our latest, most modern A320 production line opens a new chapter in efficient, digital aircraft manufacturing,” said Guillaume Faury. “With these new technologies we are building our aircraft more efficiently, a key enabler for higher production rates. I would like to thank the teams who pushed this newest Airbus production standard from concept to reality.”
With more than 14,000 A320ceo and A320neo Family aircraft ordered and over 8,100 delivered, the A320 is the world’s most successful single-aisle aircraft family. Incorporating the latest state-of-the-art technologies including new-generation engines and Sharklets, the A320neo Family provides 15 percent fuel savings at delivery and 20 percent by 2020. To date, the A320neo Family has captured nearly a 60 percent market share with more than 6,000 orders from 100 customers.
The A320 Family aircraft are manufactured globally, at Airbus sites in Europe, China and the US. In addition to the new production line, Airbus also inaugurated a larger and modernised Hamburg A320 Family delivery centre with more customer areas, more efficient delivery processes and increased hospitality services.
Background information
The line features two seven-axis robots for automated fuselage drilling. These robots are able to drill almost 80 percent of holes on the upper side of the sections, which improves the ergonomic working environment. The robots also drill with higher accuracy to ensure a constant level of production quality resulting in less rework. Furthermore, the new line features an innovative layout and the use of mobile tooling platforms that navigate autonomously with laser trackers.
The new technologies and processes applied in the new line were designed and implemented in close coordination with employees and following the principle of Design Thinking. This resulted in a modern and much more efficient working environment with an optimised provisioning of all required materials at the work stations within a range of three metres, shorter walking distances and already unpacked components ready to mount. Many of the new technologies and processes will be transferred to other Airbus production lines worldwide.
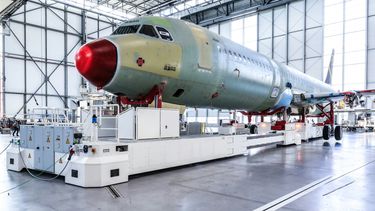
Your media contacts
Contact us
Heiko Stolzke
AIRBUS | Commercial Aircraft
Daniel Werdung
AIRBUS | Commercial Aircraft