Advancing aerospace materials
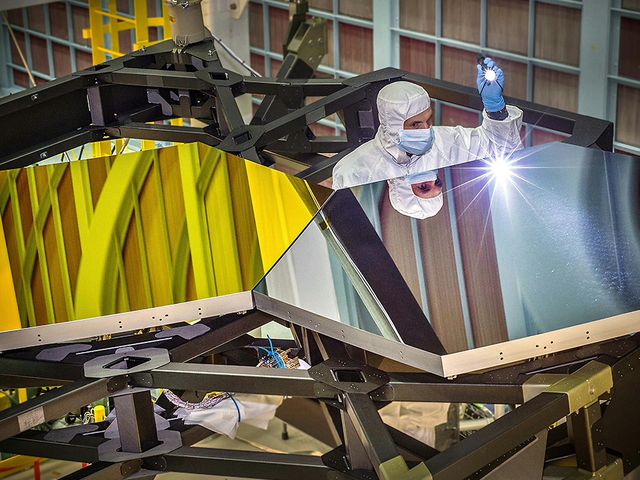
From composite aircraft to lightweight space technology, Airbus leads the way in developing advanced aerospace materials and manufacturing techniques.
Composite materials: the here and now

Thirty-two metres long by six metres wide. That’s the size of the wing for the A350-1000, making it the largest single part made from carbon fibre composite material in civil aviation. Twenty percent lighter than aluminium, no corrosion, no fatigue, less maintenance: the advantages are clear.
It’s why, in total, more than 50% of Airbus’ latest jetliner is made from composite materials. It’s also why Airbus Helicopters has created the H160, the world’s first fully composite civil rotorcraft, which is set to enter service in 2018.
From metals to carbon fibre
Not long ago, passenger aircraft were made predominantly from metals such as steel and aluminium, but the pressure to reduce weight is leading to a greater adoption of other materials, particularly carbon fibre composites.
In the past, these materials were expensive and time-consuming to produce, and were mainly found in small aircraft parts and lower-volume products such as military planes and satellites.
“Despite its obvious advantages over metals, there is still a higher degree of manual labour involved, while the material costs are also greater,” explains Christian Weimer, head of composite materials & processes at Airbus Innovations. “But the tipping point in terms of economical large-volume manufacturing is getting ever nearer.”
Driving this change are innovative automated production facilities, like the Airbus Illescas plant in Spain. When it first opened 25 years ago, workers at the facility could lay around 3kg of carbon fibre composite. Now, it produces 34kg per hour.
Partnering with the automotive industry
To ensure progress on aerospace composite materials production continues, Christian Weimer’s Airbus Innovations team is constantly searching for further improvements.
“We’re starting to work more with the automotive sector, sharing information with the likes of BMW and Audi. They have different quality and performance demands as aerospace, but they can provide interesting insights into high-volume manufacturing and maybe even new composite structural design approaches" says Christian Weimer.
Silicon carbide – Lightweight space explorer
Airbus Defence and Space's unique expertise in the field of silicon carbide is revolutionising space optics while expanding Europe’s technology base.
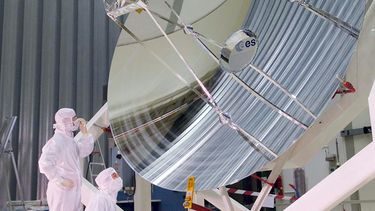
The largest mirrors in space
“It started in the 1990s: astronomical telescopes were becoming larger and we needed a new material to reduce the mirror weight,” explains Airbus Defence and Space’s Emmanuel Sein.
The answer was silicon carbide: lighter than metal or glass, it can be optically polished making it perfect for high performance lightweight mirrors. It also has excellent structural stability and thermal properties: vital for the accuracy of a telescope when temperatures in space plummet to -240°C.
New frontiers with Herschel
Having recognised the potential, Airbus Defence and Space (Airbus DS) joined together with French ceramic material specialist Mersen to form Boostec. “Our partner had experience in manufacturing small silicon carbide parts, but we were looking at dimensions of three metres or more,” says Sein.
After successfully completing a high-precision silicon carbide camera for the Rosetta mission, Airbus DS then built the Herschel Space Observatory for the European Space Agency (ESA), launched in 2009.
“The primary mirror is the largest single space telescope mirror in the world, 3.5 metres in diameter and weighing approximately 300 kg ,” says Sein. “If it had been built with standard optical materials instead of advanced aerospace materials, the mass would have been three tonnes.”
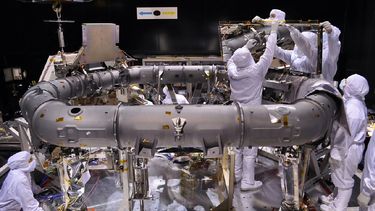
The shape of telescopes to come
Using this same expertise, Airbus DS has also built the Gaia spacecraft, launched in 2013 and made almost entirely from silicon carbide. It has the most sensitive telescope ever made and is currently gathering data for a 3D map of our galaxy.
Airbus DS is now working on part of the James Webb Space Telescope (JWST), which will launch in 2018. The company is building its NIRSpec ‘super eye’, a 200kg spectrograph made entirely from silicon carbide that will be able to detect the faintest radiation from the most distant galaxies.
Furthermore, Airbus DS is manufacturing the complete payload module of ESA’s Euclid mission, which incorporates a 1.2 metre-diameter telescope made from silicon carbide. This instrument will map and investigate the nature of dark energy and dark matter in the universe.
3D printing in space – Be AMAZEd
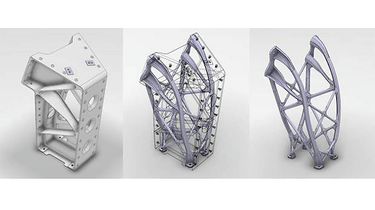
Thanks to its involvement in the European AMAZE project, Airbus is helping refine 3D printing techniques. The goal: mass-produced parts that could transform space manufacturing.
First on the scene
There aren’t many 3D printed parts in space, but Airbus Defence and Space (Airbus DS) has already established itself as a pioneer in this area of growing importance. The very first 3D printed component to make it beyond the Earth’s atmosphere was a high-strength titanium alloy bracket on-board the Atlantic Bird 7 telecoms satellite made by Airbus DS in 2011.
In 2015, Airbus DS announced the production of the first space-qualified aluminium 3D printed component for its Eurostar E3000 satellite. The part weighs 35% less than the one it replaced, with an increase in stiffness of 40%. It cannot be manufactured using conventional methods.
But despite such impressive specifications, large-scale 3D printing is not yet a reality for space materials. “We must first be able to prove the repeatability of 3D processes and our ability to consistently produce high-quality, affordable components,” explains Telecommunications Satellites R&D Manager Alan Cox.
One step closer
Enter AMAZE. Led by the European Space Agency (ESA), the project unites 28 partners across industry and academia, including Airbus. Its goal is to refine 3D printing techniques to make the mass production of space-grade metal parts a reality.
“Today we use multiple 3D technologies. Within AMAZE, for each technique, we are working on isolating factors that could negatively impact the quality of produced parts,” explains Martin Muir, Research Engineer at Airbus Innovations in the UK and contributor to the project. “Learning how to control those parameters will take us a step closer to mass-producing 3D printed parts.”
Muir expects the benefits of the AMAZE project to extend much further, though: “The pooled wealth of knowledge is enabling the project to proceed incredibly well, with applications extending well beyond aerospace.”
From metals to carbon fibre
Not long ago, passenger aircraft were made predominantly from metals such as steel and aluminium, but the pressure to reduce weight is leading to a greater adoption of other materials, particularly carbon fibre composites.
In the past, these materials were expensive and time-consuming to produce, and were mainly found in small aircraft parts and lower-volume products such as military planes and satellites.
“Despite its obvious advantages over metals, there is still a higher degree of manual labour involved, while the material costs are also greater,” explains Christian Weimer, head of composite materials & processes at Airbus Innovations. “But the tipping point in terms of economical large-volume manufacturing is getting ever nearer.”
3D printing goes to the Moon
Instead of sending materials to space, why not use local resources? Architecture firm Foster and Partners, in conjunction with ESA, is exploring the possibilities of 3D printing to construct lunar habitations using regolith, or lunar soil, as building matter.
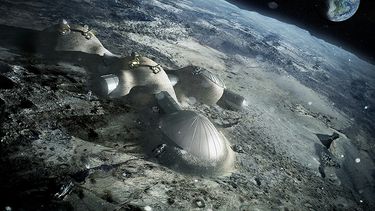