Power8 prepares way for "New Airbus"
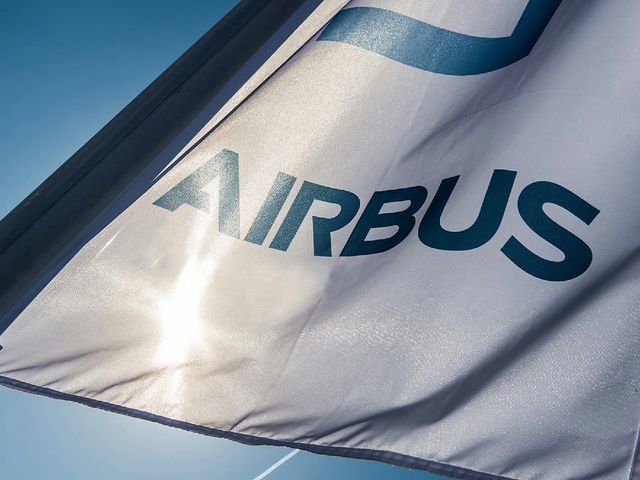
Following the unanimous approval by the EADS Board of Directors on Monday, Airbus today presented the details of its Power8 restructuring plan to the Airbus European Works Council and announced the creation of a new industrial and operating structure for the Company.
Power8 will enable Airbus to face the very substantial challenge of the US dollar weakness, increased competitive pressure, the financial burden related to the A380 delays as well as meet its other future investment needs. Power8 provides for strong cost-cutting measures, aims at transforming the Airbus business model and the development of a global network of partners. It will allow Airbus to devote its resources to core activities and eliminate inefficiencies within its current structure. The programme aims at the full industrial integration of Airbus by establishing a new industrial organization with transnational Centres of Excellence replacing the existing national structures. This transformation will happen progressively over several years and includes the further extension of Airbus' global footprint.
As part of Power8, the Airbus management will implement strong cost reduction and cash generating efforts leading to EBIT contributions of ? 2.1 billion from 2010 onwards and additional ? 5 billion of cumulative cash flow from 2007 to 2010. A large part of the cost savings will be achieved through reducing the total Airbus overhead workforce (including temporary and on-site supplier workforce) by 10,000. The envisaged measures to reduce overhead costs, and specifically headcount, require a provision of ? 680 million to be taken in the first quarter of 2007. Airbus has put in place a robust tracking system with tangible matrix regarding cost and cash impact up to their materialization in the financial statements.
Airbus has the full support of all EADS core shareholders for Power8. The EADS and Airbus management has reviewed the programme thoroughly and is convinced that the envisaged measures will deliver on its economic promises. "The core objective of the programme is to make Airbus more efficient and competitive, so as to produce the most advanced and profitable products, and to serve its customers better in the future", the CEOs of EADS Tom Enders and Louis Gallois said.
"We have had an excellent sales and delivery performance in 2006. But our long-term future is at stake if we don't act now," Mr Gallois, who is also Airbus President and CEO, said. "We fully appreciate that this transformation must be undertaken jointly and in close consultation with our social partners". Airbus will report a negative EBIT in 2006 and, following the A380 delays, faces significant cash needs and deteriorating profits in the future, together with large investments needed for current and future programmes, in particular the A350 XWB. More fundamentally, the Dollar weakness alone has led to a 20 percent loss of competitiveness in only six years versus Airbus' competition. "We cannot continue to produce at our current Euro costs and sell at Boeing?s dollar prices," he said.
"Without establishing Power8 quickly, profitability will drift significantly short of industry standards and of reasonable expectations. This is an unsustainable and unacceptable situation. Power8 is designed to reduce that gap," said EADS and Airbus CFO Hans Peter Ring.
Power8 envisages the following measures:
Lighter and cost efficient management
The objective of a lighter and cost efficient management will be addressed by several Power8 programme modules and in particular by the Reduction of Airbus Overhead costs module.
Reduction of Airbus Overhead Costs: The Airbus management proposes a progressive headcount reduction of 10,000 overhead positions over four years - thereof in Airbus Deutschland around 3,700 in Airbus France around 3,200, in Airbus UK around 1,600, in Airbus CE around 1,100 and in Airbus España around 400.
5,000 of these positions are temporary or on-site subcontractors, where reductions will begin immediately. The other 5,000 overhead positions affected will be direct Airbus employees. Priority is given to achieve reductions through negotiated voluntary severance processes and schemes in each country concerned. The respective national processes, including negotiations in each country of voluntary severance schemes, will be launched immediately. Airbus' total workforce consists of 57,000 direct employees plus 30,000 subcontractors.
At this stage, the Airbus management proposes no forced redundancies. Should these schemes not generate the expected level of reductions within the next 12 to 18 months, other measures will have to be considered to fully achieve the cost saving targets.
"We will manage the social impact of these measures properly and in close dialogue with our employee representatives," Mr. Gallois stressed. "The burden will be spread in a fair and equitable manner across Airbus. The balance of the Airbus founding nations will be preserved."
Airbus will launch a strong training initiative, to identify the skills required by the "New Airbus" and to deliver the relevant training programmes.
Other substantial cost cutting and strict budget control measures are already underway. They include a temporary hiring freeze, an executive salary freeze for 2007, as well as significant cuts in general expenses. As part of the overall cost cutting, Airbus and EADS will work together to implement the strategy of shared services and sourcing.
Further Power8 modules aimed at streamlining Airbus' processes and supporting the transition to the "New Airbus" are:
Develop Faster: This module aims at the reduction of cycle time of new aircraft development from 7.5 to 6 years, while establishing robust development processes with risk-sharing partners to secure these cycle time reductions, as well as the required aircraft maturity at entry into service. It also aims at improving the productivity of the company's engineering activities by 15 per cent.
Lean Manufacturing: It is meant to further integrate manufacturing and associated engineering, and ensure the deployment of consistent lean production principles across all plants. A productivity increase by 16 per cent is targeted by 2010.
Smart Buying: This module aims at the reduction of the Airbus supply cost base. It will also contribute to the reshaping and consolidation of our supply base, and the building of a network of strong Risk Sharing Partners to Tier 1 suppliers, while streamlining the logistics organization (from 80 to 8 logistic centres).
Maximise Cash: This module targets the reduction of financial working capital and the tight control of cash in all operations.
The Customer First Module will ensure the interests of customers to always come first. "Delivering and even improving on our commitments, serving our customers even better, with even higher levels of services, more reliability and reactivity, and further improved quality is our prime objective in all this", explains Mr Gallois.
Focus on core business
In the future, Airbus will focus on "core business" activities that are critical for the integrity and safety of the aircraft, or vital for technological and commercial differentiation, for the operability and reliability of the aircraft and its maturity at entry into service. These activities include overall aircraft and cabin architecture, systems integration, as well as the design, assembly, installation, equipping, customization and testing of major and complex components or manufacturing of new technology parts.
"This shift is essential for Airbus' future. Many industries face similar challenges, but we have to establish our own way with specific solutions. We must retain the competencies that are essential to design, develop, produce, deliver and support the best and most efficient products for our customers," Mr. Gallois said. "If we move carefully, pragmatically and quickly, we will leverage our position as a leading global player in the civil airliner market."
This "core" activity focus will be implemented in the "make or buy" strategy adopted for the A350 XWB. About 50 per cent of aerostructure work will be outsourced to risk-sharing partners (? 1.8 billion non recurring costs and ? 600 million associated CAPEX). This is proportionally about twice as much as in earlier programmes.
The workshare responsibility for the development of the A350 XWB will be split equitably among the founding nations with about 35 percent for Germany and France, 20 per cent for the UK and 10 per cent for Spain.
Long-term global partnership network
Airbus will restructure its industrial set up and establish in the coming years a long-term oriented network with strong partners. This will allow Airbus to share development costs as well as engineering resources.
"We will turn Airbus into an extended enterprise. The A350 XWB will draw on this new business model, as we assign large work packages to Tier 1 suppliers in return for a better distribution of future investment, risks and opportunities, with a consolidated supply base," Mr. Gallois said.
Airbus is considering industrial partnerships at its plants in Filton, Meaulte and Nordenham, in order to facilitate their development from metallic to composite design and manufacturing technology. The company has already received unsolicited proposals by potential industrial partners ready to invest in these sites and to possibly take partially or fully the control of them in the framework of the extended enterprise concept.
Airbus is determined to pragmatically attain the optimum scope of industrial activities and to optimize resource allocation and enhance capital efficiency. "This is the right time to consider such a partnership approach," Mr. Gallois said. "Our order book translates into more than five years of production, and customer demand continues to be very high for our aircraft. We are ramping up our production everywhere and have just launched the A350 XWB. We are ready to share attractive business opportunities with strong partners."
The sites in Laupheim, St. Nazaire-Ville and Varel will continue to perform long-term substantial workloads on the current Airbus aircraft programmes, such as the A380, the A320, the A330/A340 families, and the A400M. Airbus is committed to seeking viable future opportunities for these sites, this includes options to sell sites to key suppliers, management buy out or combination with nearby sites. This will of course be done in close consultation with the social partners.
"We will prepare the future of each and every one of our sites in the overall interest of Airbus, to strengthen industrial partners and suppliers, and to ensure long-term local business and employment continuity," said Mr. Gallois.
Streamline the final assembly lines
A number of measures are also being implemented to further increase the efficiency of the final assembly lines (FALs).
The A350 XWB will be assembled and receive its interior furnishing in Toulouse, in the same facilities as the current A330/A340, enabling a capacity enhancement of this FAL.
A third A320 Family FAL will be set up in Hamburg immediately to cope with the steep production ramp-up currently under way. This FAL will be established in already existing facilities and will have full type flexibility when demand for A320s exceeds rate 14 per month. The A320 will continue to be assembled in Toulouse up to rate 14. Hamburg will also perform final assembly of the future New Single Aisle family.
Furthermore, in order to allow parts to be fitted in the most logical place to optimize the overall cycle time, some upstream preparatory A320 and A380 cabin installation work will be transferred from Hamburg to Toulouse. Cabin installation will remain in Hamburg. A380 deliveries will still be made from both Hamburg and Toulouse.
Fully integrated and transnational organisation
Airbus will introduce a fully integrated and transnational organisation to support the implementation of Power8 and the establishment of the new business model.
This new organisation will enable cost savings and strengthen leadership through clearer accountability, faster decision-making and simpler interfaces.
"Integration means strengthening the accountability of those responsible. It is not an invitation for centralisation or doing everything in-house. On the contrary, we demand an empowerment of those in charge," Mr. Gallois explained.
The new industrial organisation will force process streamlining through the establishment of four truly transnational "centres of excellence" led by the Head of Operations: Fuselage & Cabin, Wing & Pylon, Rear, and Aerostructure, the latter being in charge of fuselage subassembly and interior furnishing activities. This will replace the current organization of eight nationally structured centres of excellence.
Further organisational changes include completing the integration of support functions such as Finance and HR as well as reinforcing the authority of core functions such as Engineering, Procurement and Programmes.
The national entity leaders will assume a strong representative role, acting as Airbus ambassadors. They will be accountable for all aspects connected to national regulations (legal, social etc.) but will not have any operational responsibility. They will report to the Airbus CEO office and act on its behalf.
Sharing services with EADS corporate functions where clear benefits arise, will be another lever to improve the efficiency of the support processes, optimize resources and reduce overhead costs.
Concluding his comments, Louis Gallois said: "None of these changes will be easy, but they are essential to securing the future of Airbus as a world-leading aircraft manufacturer for the long-term, and a business of which all its stakeholders can be rightly proud."
Airbus operates in a growth market of 22,000 new aircraft in the next 20 years. The order backlog represents about five years of future production, and the company continues to deliver record levels of aircraft.
EBIT
Develop Faster
6%
Smart Buying
31%
Lean Manufacturing
16%
Reduce Overhead
32%
Maximise Cash
-
Restructure Industrial Set up/Focus on Core
12%
Final Assembly Line
3%
Total
100% Airbus is an EADS company.