Hangar of the future
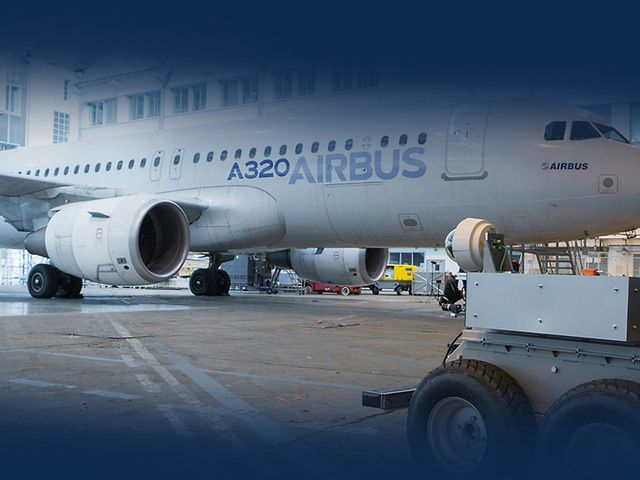
Airbus aims to reboot the MRO sector with its Hangar of the Future, an innovative application of state-of-the-art technologies and methods aimed at increasing operational efficiency for customers’ aircraft and rotorcraft worldwide.
MRO providers in Singapore have a problem: airlines are going elsewhere for their maintenance and repair. “Indonesia, Thailand and the Philippines are drawing MRO [Maintenance, Repair and Overhaul] business away because they’re cheaper,” explains David Woon, Hangar of the Future project manager. “And because of this intense competition, Singapore's MROs don’t have the time or money to invest in new technologies.”
In February 2016, the Singapore government enlisted Airbus to help local MRO providers improve productivity, with the intention of setting up a testbed where new technologies can be tested in a research environment. By October 2016, Airbus’s Hangar of the Future project was underway.
Responding to change
At its inception, the Airbus Innovations-led Hangar of the Future concept aimed to increase operational efficiency in MROs by applying both the Group’s lean management experience and proven state-of-the-art technologies to the maintenance sector. Ultimately, the Hangar’s revamped MRO services will be a crucial step in providing the Group’s customers with end-to-end solutions. "Today, instead of selling the aircraft and support package, we’re often contracted to provide mission availability", says Pierre Nicoli, Head of new services development at Airbus Helicopters.
MROs are facing a rapidly changing business environment. As Pierre Nicoli, head of new services development at Airbus Helicopters explains, customer contracts are changing. Whether it’s a search and rescue operation that needs aircraft on demand, oil and gas sector helicopters logging more than 2,000 flight hours per year, or militaries facing budget cuts who need to optimise their limited fleet, implementing a more efficient maintenance process translates into securing the same availability and capability with fewer helicopters – a big benefit for operators.
A new perspective
While Airbus isn’t new to lean manufacturing, having benefitted from its application across the Group’s final assembly lines (FALs), the concept of creating more value for customers with fewer resources is new to MROs. “It’s a different philosophy,” says Christophe De Flaugergues, who manages functional knowledge for Airbus’ e-solution organisation.
Ideas like bundling tasks – e.g., repairing two different parts located under the same panel at the same time – are easily translatable from one environment to the other. However, the more predictable structure of the FAL, with strict processes and few unexpected events (because the aircraft are not flying), is different from MROs, full of shifting circumstances that require plans to be revised.
Nicoli notes that there are also differences between airplane and rotorcraft maintenance, both of which the Hangar of the Future aims to tackle. “We don’t always land in big airports with big hangars, but could be anywhere from industrialised areas to deserts.” In addition to expediting daily operations, when aircraft require servicing in remote locations, cutting-edge technology is vital.
Aiding the experts
Technologies developed and knowledge gathered by De Flaugergues’ and Nicoli’s teams will be translated into the initial demonstrator phase of the Hangar of the Future. Maintenance mobility, for example, currently deployed at JetBlue, will transition from a data-collection tool for airline operations to a task-execution monitoring tool for MROs, delivering valuable maintenance information to technicians before the aircraft has even touched down.
“Hopefully, maintenance operators are experts,” says François Guillaume, Hangar of the Future’s technical lead. But the difficulty is in the context. It’s easy to waste time locating the equipment and information needed to prepare the task. Guillaume describes augmented reality (AR) and virtual reality (VR) as the perfect technologies to build a bridge between physical products and the digital world. In the case of a stalled helicopter in the desert, for example, AR would be a crucial way to guide technicians through a rare repair. "Maintaining an aircraft doesn’t usually happen in a nice office with air-con and good light – you have time pressure, it’s dark, it’s raining, and the operators themselves trained on different aircraft – there are a lot of constraints", says Guillaume.
Automated non-destructive testing (NDT) in this case, an inspection scan of the aircraft upon entering the hangar – will allow experts to concentrate on defect analysis and classification instead of searching for data. The Internet of Things concept, integrated through RFID technology, will be used to identify and track tools and parts. It will be interfaced with the supervision module in a ‘control room’, which helps operators and customers follow activities performed on the aircraft and anticipate modifications.
Drones and robots will also enable the Group to obtain information and specificity it has never had before, like aircraft structure, flight hours, and issues accumulated over time.
“The Air-Cobot robot, currently designed for inspecting aircraft from the ground, could be connected with a flying drone to access the top of the aircraft and speed up the data capture (from 2 hours with conventional means to 15 minutes). EasyJet is testing drone inspection today, and we are also testing them on the A330 FAL through the Aircam project. We will also try to use drones to accurately size up the damage and earlier identify unplanned repairs,” says De Flaugergues.
With this input populating a collective database, Airbus will be able to better predict future issues based on past issues and maintenance. “By integrating physical software, we’ll enrich the way we predict unexpected events.”
Proof and partnerships
The Hangar of the Future’s test bed component not only offers an easy way to test and develop new technology, it also enables any of the Hangar’s project partners – from local Singaporean start-ups to companies like 3M – to come in and interface with this technology in a real hangar and real aircraft.
To be as efficient as possible in the digital environment, says De Flaugergues, harnessing data is key. “The Hangar of the Future, in connecting the maintenance information system, the physical means, the software and the aircraft, generates a lot more information than we have today. Once we are able to analyse this new data and cross-reference it, we can provide better predictions.”
“This initiative is unique and totally unprecedented in Airbus Singapore,” says Woon, “because it combines the ingenuity and efforts of several business divisions – Airbus Services Asia Pacific (ASAP), Satair, TESTIA Asia Pacific and Airbus Helicopters Southeast Asia (AHSA) – in one single endeavour. We’re integrating and deploying new ideas into a real hangar environment, close to our customers.”
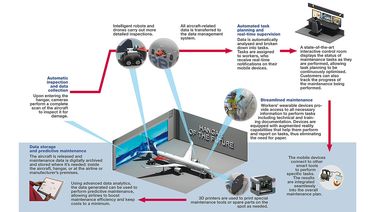
Jess Holl