The European Union member states have set themselves the objective of developing a new generation of aircraft that will deliver a 50% reduction in fuel consumption and CO2 emissions to mitigate climate change by 2020. Known as Clean Sky, this major initiative aims to review the thousands of components used in current aircraft and helicopters to identify areas that can be significantly improved.
One of the EU’s largest and most ambitious innovation projects, Clean Sky’s current phase involves 600 organisations from 24 countries and has a budget of over €4 billion. Airbus is one of the 16 industry leaders involved. “It can take up to 10 years to test and mature safe, efficient and reliable technologies to build new aircraft, and Clean Sky provides the right framework to do just that,” explains Jens Koenig, coordinator of Airbus research and technology for the Clean Sky project.
Powering up the future
The project’s flagship is a new large passenger airliner that incorporates significant changes compared to the models passengers fly in now. Its most striking feature is 2 large open rotor engines, constituted of 2 rows of contra-rotating propellers that are positioned at the end of the fuselage.
While this configuration considerably reduces fuel consumption, it requires changes to the fuselage design and to the position and shape of the wings. Due to the challenges this concept poses, very large ultra-high bypass ratio turbofan engines for next generation aircraft are also being developed in parallel as an alternative.
Cutting the drag
Another area of exploration is possible ways to reduce aircraft drag. This is the aim of BLADE, a project headed by Airbus to design a new kind of laminar wing that displaces turbulence “as far as possible from the wing’s leading edge,” in the words of project leader Daniel Kierbel.
By modifying the shape, materials and surface of the wings, fuel consumption can be reduced by 4.6%. “That may not seem like much, but when it’s multiplied by the potential number of short-range aircraft currently in operation around the world, it starts to become really significant,” he points out.
In a hangar in Tarbes, France, an Airbus A340-300 has literally had its outer wings cut off. This test aircraft is one of 2 ‘Flight Labs’ provided by Airbus to test high potential technologies being developed within Clean Sky. The outer wings of Flight Lab 2 will be replaced with 2 types of laminar wings, one on each side. Geometrically identical, each one is based on a different structural concept.
The team aims to perform the first test flight in the second half of 2017 and, according to Kierbel, these types of technologies could be incorporated into commercial aircraft in the near future. Another visible difference is that these new wings have fewer fasteners on the upper covers than traditional ones. “This helps them achieve a better laminar flow, thanks to their smoother surface,” Kierbel explains.
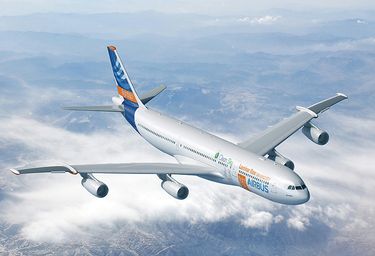
Pilots at heart
"One of our aims is to reduce pilot workload by creating new automatic systems that reconfigure the aircraft in the event of a failure", says Miguel Llorca, Head of military aircraft research and development at Airbus Defence and Space.
To bring down transport costs and further reduce CO2 emissions, there is also a need for new regional aircraft with seating for around 100 passengers. New prototypes developed by Airbus Defence and Space introduce wing structure changes and flight physics optimisation to reduce aircraft weight and fuel consumption as well as changes to the flight cabin and aircraft handling – all of which will be tested on a C295-P1.
Airbus Defence and Space leads the project to modify the structure of the new aircraft, which will also be equipped with turboprops. “We’re also exploring new systems that allow pilots to give orders to the aircraft through voice recognition, or presenting flight information to pilots through light head-mounted displays such as Google glasses,” says Llorca.
Electrical innovations
On-board electronics is another area with great potential for improvement. Recently, Airbus’ Flight Lab 1 – involving a consortium of 9 companies and institutions in 5 countries – performed flight tests for 5 new innovative electrical technologies mounted on an A320.
These technologies included a new air intake with protection against ice build-up during flight, a new air conditioning system that draws air from the exterior and not from the engines as in current systems, and various other electronic systems that significantly reduce the noise levels generated by conventional devices.
“This year we’ve completed more than 300 hours of ground tests and 27 hours of flight tests using a total of 400 sensors and 18,000 new parts. It’s been a resounding success and we have learned a lot that we can apply going forward,” explains project leader Jonathan Rigaud.
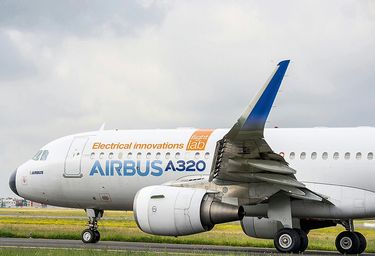
A new breed of aircraft
The consortium is also exploring potential civil applications for new hybrid helicopters based on Airbus Helicopters’ X3. These aircraft combine the hover flight characteristic of helicopters with the speed of a passenger aircraft, reaching speeds 50% faster than conventional helicopters.
‘Green rotors’ also significantly reduce engine noise and cost per passenger. One of the programme’s objectives is to adapt these new aircraft to civil uses, particularly search and rescue and emergencies. “The hybrid concept allows us to extend the radius of action by 50%, resulting in substantial economic benefits for operators as they can allow themselves to have fewer bases and fewer aircraft – not to mention how many lives they can save in time,” explains Tomasz Krysinski, head of research and innovation at Airbus Helicopters.
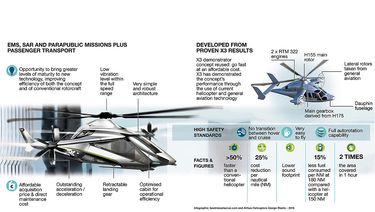
From research to reality
This current phase of the project, Clean Sky 2, is reviewing and improving practically every component, every manufacturing stage and every use being made of aircraft. For example, one project is exploring the concept of ‘talking’ aircraft that provide continuous updates of their technical status, which could lead to a reduction in the number of routine checks and their cost.
Another concept set to change is the idea that an aircraft should be made up of thousands of different parts with a complex configuration of cables in its interior that needs to be connected in the assembly hangars.
"We’re looking to design the fuselage of the future, with much more automated production", says Koenig. Clean Sky 2 is currently developing all these and other technologies with a view to their incorporation into commercial aircraft by 2025. Koenig considers that the changes, although gradual, will be important: “When you think about the aircraft of the future, people tend to imagine something like the Starship Enterprise. In reality, we think they’ll be quite similar to current aircraft with wings and engines, but much quieter and much more efficient.”
Nuño Domínguez