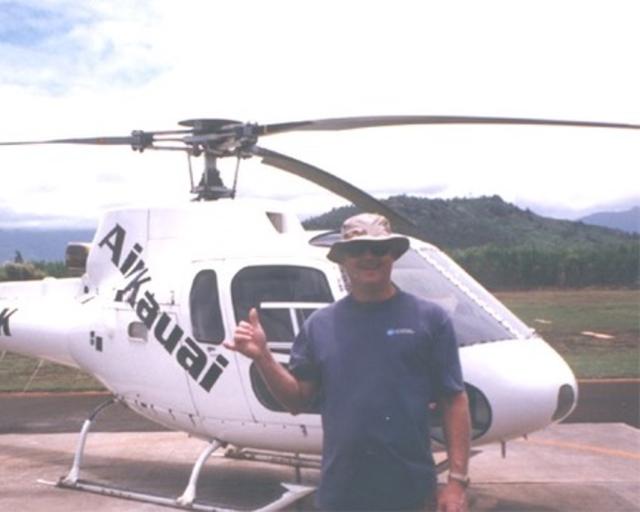
There is no mission impossible!
Airbus Careers catches up with Thomas Brown to celebrate his 50th anniversary as an Airbus employee and to learn more about his incredible aerospace journey. Throughout his career, Thomas has played an important role at Airbus Helicopters in the U.S., having contributed his expertise and dedication in various roles over the years. Get inspired as he tells his story in his own words.
Back to the beginning
In April 1973, right after turning 21, I began my journey with Vought Helicopters. Starting as a mechanic on the shop floor, I worked under the manager of New Helicopter Completions.
Our task was to assemble helicopters that arrived in large boxes. Once assembled, we installed additional features, conducted flight tests, and flew the helicopters for painting. Finally, we would fly them back to the plant for customer delivery. As technicians, we did more than just mechanics' work – we handled everything from sheet metal installation to flight tests and customer delivery.
It was a challenging and rewarding experience that shaped the beginning of my career in the aerospace industry.
Early recollections
I had the privilege of being part of the team that created the first IFR Gazelle. Once the local flight tests were completed, I accompanied the aircraft to obtain FAA approval. Shortly after, I landed a job in Technical Support, where I underwent training in France for the SA330 Puma airframe and in Bordes for the engine. At only 23, I was learning many new things very quickly.
When I travelled to visit customers, I relied on others to pick me up since I wasn't old enough to rent a car. It was amusing how some customers would inquire about the Tech Rep's whereabouts upon my arrival. They believed that if I was not old enough to rent a car, then I couldn’t possibly possess the knowledge to fix their aircraft.
In Tech Support, our role extended beyond being Tech Reps for the engine and airframe; we also served as training instructors. We wore many hats to support our customers. During my time as a Tech Rep, I visited 49 states across North America.
Reaching new career heights
Once our facility relocated to the current location on Forum Drive in Grand Prairie, TX, I was promoted to Production Manager responsible for overseeing the manufacturing of all new aircraft. It was an incredible experience.
Later finding myself as the manager of the blade shop, I went on the road to visit customers and submit bids for repairing and overhauling their damaged aircraft, which would then be brought back to Airbus. I created, made, and delivered a catalogue of the diverse capabilities of the different shops.
An opportunity to do things and see places I never dreamt possible
Surviving natural disasters
In 1992, when Aerospatiale and MBB merged, my position as manager of the MRO department changed to Marketing Specialist for the MRO (Maintenance, Repair and Overhaul) team. That year, two hurricanes hit the U.S. - Hurricane Andrew hit Florida and Hurricane Iniki hit the island of Kauai.
Despite the challenging circumstances, I flew to both locations to ensure the smooth operation of services. It was a demanding task, but I managed to effectively keep things running amidst the aftermath of these natural disasters.
In 1994 the Northridge earthquake happened. I was asked to go to Los Angeles and support the LAPD (Los Angeles Police Department) at Van Nuys Airport. I had never experienced an earthquake before, but, while I was there, I did feel several aftershocks. The MRO department was able to make repairs and ship them to the LAPD to get the aircraft back up.
Back to the future
In 1995, I was transferred back to field service to be an in-house representative. I was promoted to a field rep, where I am today.
During this period, I was assigned to Maui Blue Hawaiian Helicopter to provide support for the first customer-owned EC130 (now known as the H130). In 2002, a steady control for track and balance, along with hammer adjustment, was developed in France. I drove across the United States, adjusting hammers on various aircraft.
Additionally, Helibras, an Airbus manufacturing division in Brazil, requested our assistance with adjusting hammers on the EC130s and several H120s by sending the Steady Control to their facility.
In December 2003, I was asked to move to Las Vegas to be the Tech Rep supporting the tour industry and maintenance needs in Hawaii. The new areas I started to support were Colorado, Utah, New Mexico, Arizona and Nevada.
No mission is impossible
In April 2017 I got the honour of working and supporting the Mission:Impossible-Fallout H125 aircraft on location. I started in England then went to France. The ship was then sent to New Zealand for all the flight scenes. That was a lot of fun. This gave me the opportunity to get to know the ab H125 better. As a rep we do not get to spend much time doing hands-on work, just mostly troubleshooting. This was a very good time for me.
A passion for aerospace
I never thought that I would ever get to do what I have done. Vought, and later Aerospatiale and Eurocopter, the foundations for Airbus Helicopters, gave me the opportunity to do things and see places I never dreamt I would.
I get asked why I stay with the same company for so long. The company pays me to do what I enjoy doing. I have never stopped learning.